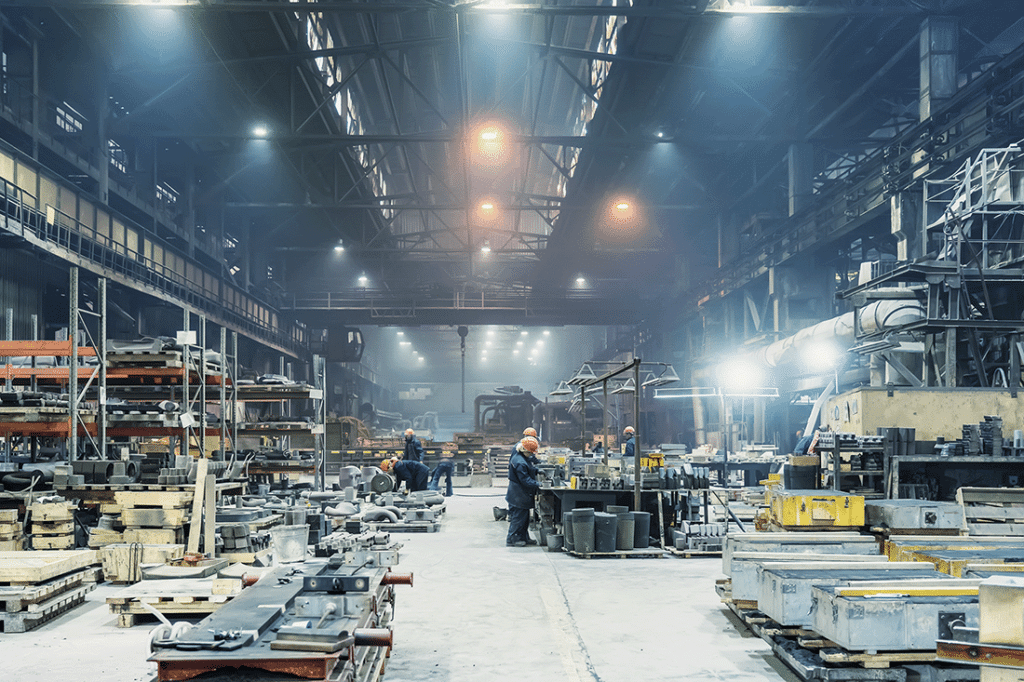
Real Time Location System (RTLS) refers to technologies used to locate an object in real time. Redundant Radio Localization Technology (RRLT™) is WISER’s patented Ultra-Wideband-driven (UWB), real-time location and tracking system. Unlike RFID or a barcode where you need line of sight to scan and identify an object, the WISER UWB RTLS system provides current location and identity without line of sight between the tag and antenna. This data is then paired with other systems to incorporate other data like batch identification, storage parameters, expiration dates, etc. The system delivers data identifying precisely where an object is at all times. Some RTLS technologies, like WISER’s RRLT, can be paired directly with identification-only systems, such as barcodes or RFID. A paired solution knows not only where the bin of products is located at any given moment, but also which/how many items may be in the bin. RTLS systems, both paired and un-paired, can be immensely powerful tools for deriving work in progress (WIP) metrics that drive process improvements and improve productivity and the bottom line.
Almost by definition, WIP involves multiple moving pieces. The scope of this juggling act can pose significant challenges for manufacturers, such as forecasting product completion, maintaining the right balance between enough and too much inventory, and identifying sources of inventory loss or damage.
Manufacturers of all sorts have implemented various tools for WIP, asset tracking, and related process improvements. These range from clipboards to spreadsheets and dedicated WIP software and hardware solutions. The purpose of these WIP tracking measures is typically to deliver the following benefits:
- Cutting down the time spent on reporting
- Keeping a better pulse on product quality parameters
- Gathering fresh data on production cycles and schedules
- Identifying bottlenecks and choke points
- Auto-tracking inventory
- Preventing unplanned downtime
- Clarifying opportunities for improvement
- Increasing productivity—and revenue—overall
WISER’s RTLS RRLT system provides for all of the above, and its use of UWB makes WISER’s technology the most precise solution available, and the only technology on the market that can track thousands of items such as work orders and assets simultaneously in real time with minimal infrastructure.
Where previous generations of tracking technology enabled location accuracy within several meters, WISER’s UWB can often deliver location accuracy within inches.
If WISER’s focus on location data sounds like GPS, it’s worth noting that UWB is an inherently short-range wireless band technology. Within the wireless spectrum, shorter ranges and emission requirements allow for low power consumption, making data inherently difficult to intercept, and thus more secure. Inherently low-power combined with more accurate localization makes UWB an ideal wireless technology for precise location-based services.
As with other industrial automation technologies, a key benefit of RTLS in manufacturing is its potential to automate, supplement or even eliminate many manual, error prone processes. Scanning is a good example. Some factories install stationary automatic scanning stations or portals for every key step of their manufacturing journey, so that batches or individual components have a clear marker of progress and compliance at each juncture. However, the limitations of scanning technologies, plus the costly physical requirements of many manufacturing processes, make automatic scanning a challenging undertaking, and often impossible.
Many manufacturers compensate for this by implementing manual scanning and data-entry processes to track WIP. These processes are nonetheless prone to human error.
WIP Tracking in a Metal Finishing Plant
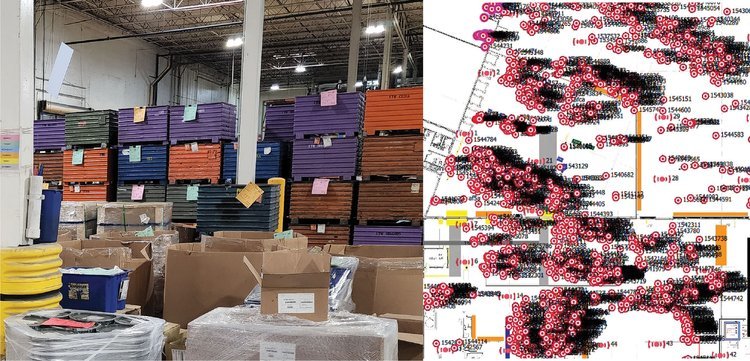
Where WISER’s RRLT locate-and-track technology has no peers, is in manufacturing environments that are cell-based, where processes are often difficult to monitor, due to the various steps a work order may take through the process. Where each job may be processed through multiple stations in various orders. Sometimes skipping stations or repeating stations. Because this manufacturing process is so flexible, it is the most complex to manage and any inefficiencies can yield huge increases of lost inventory, wasted time and ultimately money. Thus, the returns stand to be even higher for work that doesn’t necessarily follow a set sequence of steps, locations, or events.
Take for example, SWD, Inc., WISER’s customer that finishes customized metal parts. In a day, they may receive 500 orders for metal plates, specialized springs, bolts or screws, and other customized parts in varying amounts. The company’s ability to simultaneously track thousands of work orders in real time is critical to operating efficiently and maintaining customer satisfaction.
WIP Example
Below we provide an example and possible scenario on any given day in a job shop to illustrate how complex the process may be.
Order B is a group of screws that need to be heat-treated, coated, and sorted among other treatments. They must complete Stations 1, 3, and 5 before inspection and shipping.
The order easily passes through Station 1, but the worker at station 3 is busy with another order and puts Order B to the side. Things must wait which is common on a flexible job shop floor. A problem arises if Order B gets in the way of someone else working on Order C. Order B gets moved. After a few more rounds of waiting, Order B can get shuffled far from station 3 and eventually lost. The highly skilled worker at Station 3 now needs to leave her station to search for Order B which was skipped. This now delays work on all the following orders at Station 3. Searching for Order B wastes motion for that worker and causes unnecessary waiting.
No barcoding or RFID will find a lost or misplaced item, and sequential station checks are a time-consuming process without location information. RTLS solutions, however, such as the newly released high-density WISER ATLAS solution, will tag Order B’s container so it can be tracked in real time. The worker can then simply look up the location of that order on an app and find it in an instant.
With RTLS, Order B is found quickly, and the worker completes it at Station 3 before moving it on to Station 5.
You can see more of this scenario on our Work-in-Progress Tracking page.