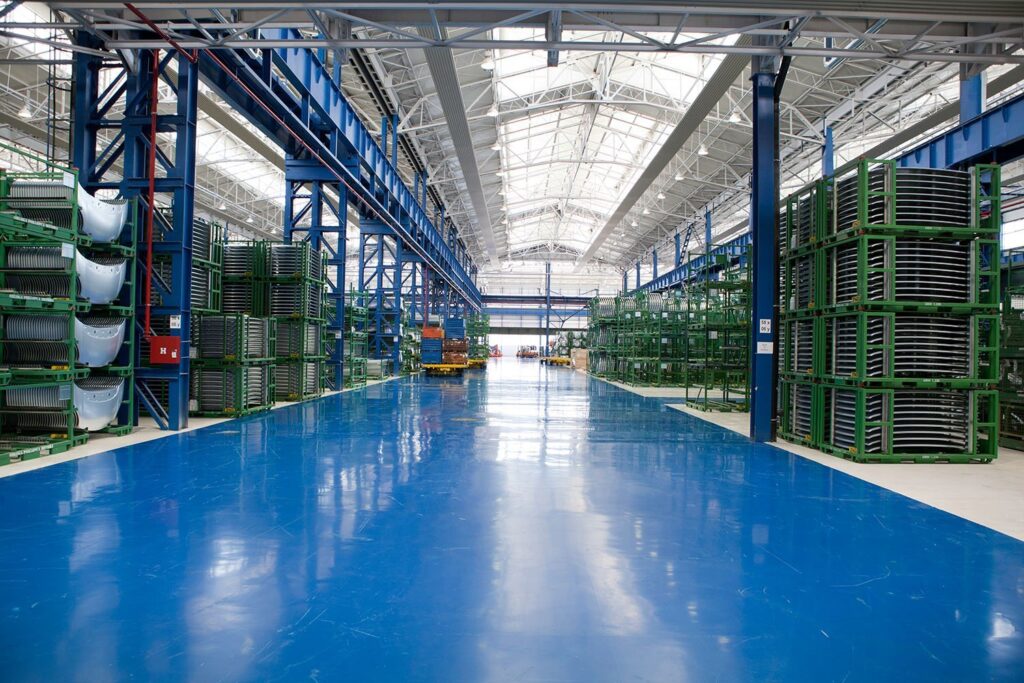
Maximizing Asset Tracking Efficiency
Here’s how your organization can utilize both ultra-wideband technologies and radio frequency identification.
As Factory of the Future and Industry 4.0 innovation deployments gain momentum worldwide, real-time location systems (RTLS) are becoming increasingly recognized as among the most productive, cost-effective, impactful and least disruptive additions to the manufacturing process. With this in mind, many companies are now faced with deciding which RTLS technology best fits their needs.
There are a variety of RTLS solutions available, including Wi-Fi, Bluetooth, ultra-wideband (UWB) and radio frequency identification (RFID). However, not all these technologies deliver results in the same way. This article will delve into the differences between these RTLS technologies and how a combination of UWB and RFID systems can produce results that are greater than the sum of their parts. It will also explore how UWB can be seamlessly integrated into RFID with minimal effort and disruption to ongoing operations. Additionally, it will provide case studies that demonstrate the significant boosts in operational productivity that can be achieved using UWB and RFID in combination.
Comparing RFID and UWB Tracking Solutions: Key Differences
Choosing the right asset-tracking technology depends on your specific needs and goals for end use. Factors to consider include the desired accuracy or granularity of location data, update rates for each asset being monitored, the number and value of assets being tracked, the costs or risks associated with asset loss, the physical environment in which the tracking will take place, and the ease of use and cost of the technology, as well as requirements for collecting and transferring data.
RFID Technology
One popular asset tracking technology is radio frequency identification. RFID has been used in a wide range of applications. RFID systems can be configured in a variety of ways, including low-frequency (LF), high-frequency (HF) and ultra-high frequency (UHF) systems, as well as passive and active systems. Passive RFID offers the ability to track a wide range of physical assets with very small and inexpensive tags. Active RFID systems can be more autonomous and less obtrusive.
Advantages of RFID include hardware interoperability, inexpensive tags (especially passive ones), various tag options and a small radio signature. However, RFID also has some disadvantages, such as variability in precision, high reader costs, complex system installations, limited coverage areas, and the potential for wireless signals to be intercepted. RFID systems are a diverse set of technologies with varying capabilities depending on their readers.
Handheld readers coupled with passive tags are very common and have minimal infrastructure requirements. Passive systems utilize very small and inexpensive tags to track a wide range of physical assets, from large vehicles and machinery to small hand tools. These systems are highly scalable, but tracking is only known as of the most recent registered point-of-scan. For real-time location, numerous scans or portal-type stationary scanner are needed across the tracking area. RFID systems, whether passive or active, works best with line-of-sight and have limited range compared to UWB-type RTLS.
UWB Technology
Ultra-wideband is a cutting-edge technology in the realm of asset tracking and real-time location. It has rapidly emerged as a leading solution for its accuracy, scalability, security and cost-effectiveness. UWB technology transmits data over a broad section of the radio spectrum using short pulses with low power output over a large bandwidth. This low-power method enables the transfer of a substantial amount of data, resulting in high accuracy real-time location determination, even without direct line of sight.
UWB boasts several advantages, such as its ability to transmit data through walls and obstacles, provide real-time updates, non-interference with most other RF signals and devices, unique radio signatures, and improved ability to avoid multipath propagation. As a result, the solution works even in cluttered industrial environments with reflective metal surfaces. However, UWB also has some drawbacks. It’s a newer RTLS technology, so industry standards and protocols for interoperability are less mature and it has less market recognition.
UWB technology is ideal for use in heavy industries and GPS-occluded environments where other wireless technologies often fail. Applications such as tracking high-value assets, or scenarios in which accuracy is crucial, such as safety, security and healthcare, offer the fastest return on investment for UWB. Its ability to work around and through obstacles offers flexibility in installation, including the ability to operate without line-of-sight between readers and tracker devices. Additionally, its unique radio signature makes it particularly well-suited for use in environments with metal and other reflective surfaces.
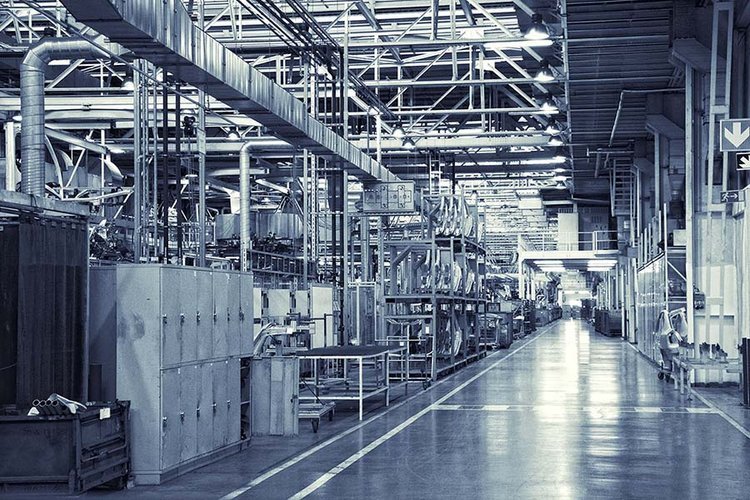
Solutions like Wiser Systems’ ATLAS & Locator Redundant Radio Location & Tracking (RRLT) technology feature an auto-calibration process making even large-scale installations quick, efficient and inexpensive. Additionally, power-saving measures, such as programmable notification rates, have been developed to extend tag operation for years without battery recharging or replacement.
When to Utilize Both RFID and UWB
In certain manufacturing facilities, combining RFID and UWB technologies can offer a comprehensive solution for asset tracking. With the presence of both high- and low-value assets, this combination can cater to different tracking requirements. Passive RFID, in particular, can provide an effective and affordable solution for tracking many low-value items, while UWB RTLS is often more accurate and can provide real-time visibility without line-of-sight for larger and more valuable items.
Optimizing Warehouse Operations with RFID and UWB Forklift Tracking
Manufacturers are leveraging the benefits of RFID technology by equipping their forklifts with RFID readers to scan pallets with RFID tags and accurately match materials to their respective locations by scanning the warehouse racking. To further enhance efficiency and optimize route management, incorporating UWB technology into forklifts, so that their real-time location and movement histories are available at a moment’s notice, is becoming a common practice among leading manufacturers.
Maximizing Automotive Manufacturing Efficiency with RFID, Barcodes and UWB Tracking Solutions
Automotive and other heavy equipment manufacturers are achieving productivity enhancements tracking of work-in-progress (WIP) items using passive RFID tags or barcodes, scanning them as they are placed on work carts or travelers, then utilizing UWB tags to always know the locations of the carts or travelers. This is ideal for automotive manufacturing plants with metal racks holding 25 to 30 parts that are moved by AGVs or robots, for example, where coupling UWB and RFID creates a system that can track the movement of AGVs, parts and item-level inventory. By tagging more than 5,000 metal racks and using barcodes for inventory management, companies can enhance facility efficiency by achieving real-time visibility over rack location and contents, as well as other moving assets (robots, tugs, buggies, etc.) with tagged contents.
Streamlining Linear Manufacturing with RFID and UWB Asset Tracking
Tracking vehicles and their components in linear manufacturing using RFID or barcode tags affixed to the vehicle’s chassis can help to maximize efficiency in a liner manufacturing environment. With RFID, you can identify vehicles and components at each production zone with stationary readers mounted close to the tags, which have a read range of typically less than 3 inches. UWB tags matched with VIN numbers will allow you to granularly locate specific vehicles indoors or outdoors in real time, with ease upon completion. This comprehensive solution ensures vehicles being stored while waiting for components or modifications have complete visibility.
Enhancing Tool Tracking and Management with RFID and UWB Technology
When facilities have a large number of tools, some of which are small and others large, utilizing both passive RFID and UWB technologies provides a complete tracking solution. RFID is perfect for monitoring and managing smaller items and hand tools in your facility. For example, a toolbox equipped with RFID readers reads the RFID when a tool is checked in and out, and also logs who took it. UWB technology is best for larger items like the toolbox and tools that cannot fit in the toolbox, allowing complete visibility and location tracking anywhere throughout the facility. For facilities without toolboxes, UWB can be used to track calibrated tools stored in closets and checked in and out daily, ensuring their whereabouts are always known.
Maximizing Manufacturing ROI and Efficiency with the Right Asset-Tracking Solution
As the adoption of asset tracking to improve manufacturing efficiency continues to gain momentum, it is important for manufacturers to consider the potential benefits of a hybrid solution that meets their specific needs. With a combined RFID-UWB approach, manufacturers can optimize cost-effectiveness and reap the full benefits of asset tracking in their facility.
Utilizing Only UWB: Case Studies
The manufacturing environment poses unique challenges for implementing an RTLS wireless radio-based system, as achieving high accuracy and adaptability can be difficult. In particular, facilities that feature metal and reflective surfaces must carefully evaluate the RTLS solution to ensure it can function accurately, securely and flexibly in this type of setting, while also supporting both indoor and outdoor operation, if necessary, and scaling to meet the needs of the facility. Unfortunately, many systems fail to deliver reliable and accurate performance in such complex and reflective environments.
For these reasons, UWB technology represents the ideal solution for RTLS in crowded and challenging manufacturing environments like factory floors. This technology enables high accuracy and reliability, even in the presence of reflective surfaces, and can scale effectively to handle thousands of assets. To illustrate this point, consider the experiences of two customers who exclusively leveraged UWB technology in their manufacturing facilities.
Workflow Management Inefficiencies in Part Tracking at GE Aviation’s MRO Facility
At GE Aerospace’s maintenance, repair and overhaul (MRO) facility, ACSC, the management of parts and work order flow was a major challenge that needed urgent attention. Each day, the team had to check the status of more than 2,000 work orders manually to prioritize their tasks for the day. This time-consuming task required 12 people to spend three hours each day, looking for the work orders that had moved to the next station the previous day.
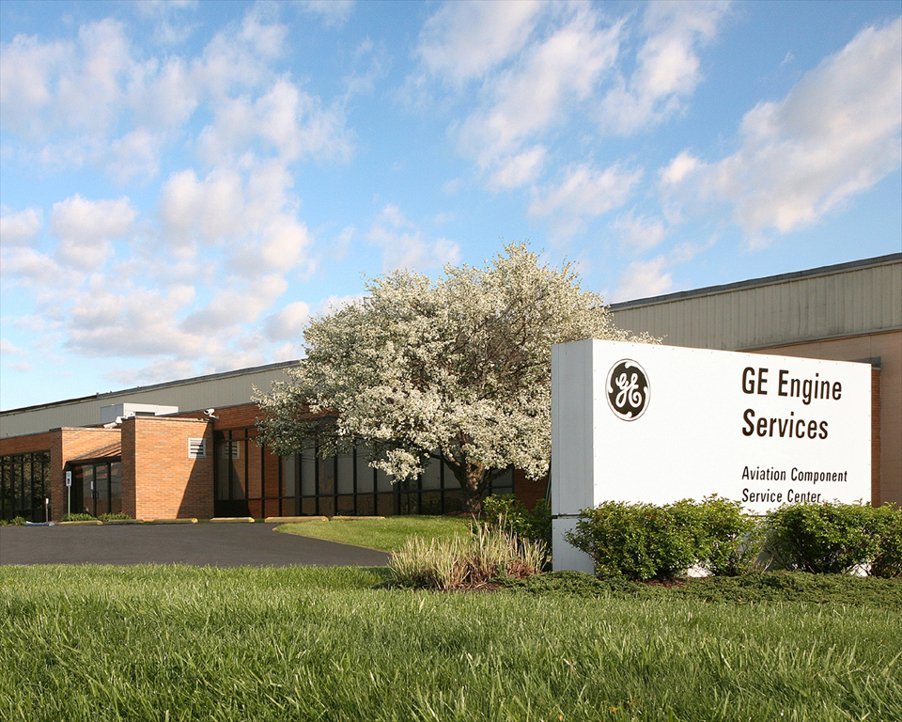
To address this problem, ACSC required a location system that would accurately and efficiently track the locations of its work orders in real time. Automating the prioritization process would eliminate the need for manual tracking and save valuable time for the team. Additionally, a simple and easy-to-use system would help to reduce errors and ensure that the team could locate parts quickly when needed.
By implementing a reliable and efficient location system, the GE Aerospace facility would be able to improve workflow management, increase productivity and reduce costs. This would allow the team to focus on providing high-quality maintenance services to their clients, ensuring that their aircraft operate safely and efficiently.
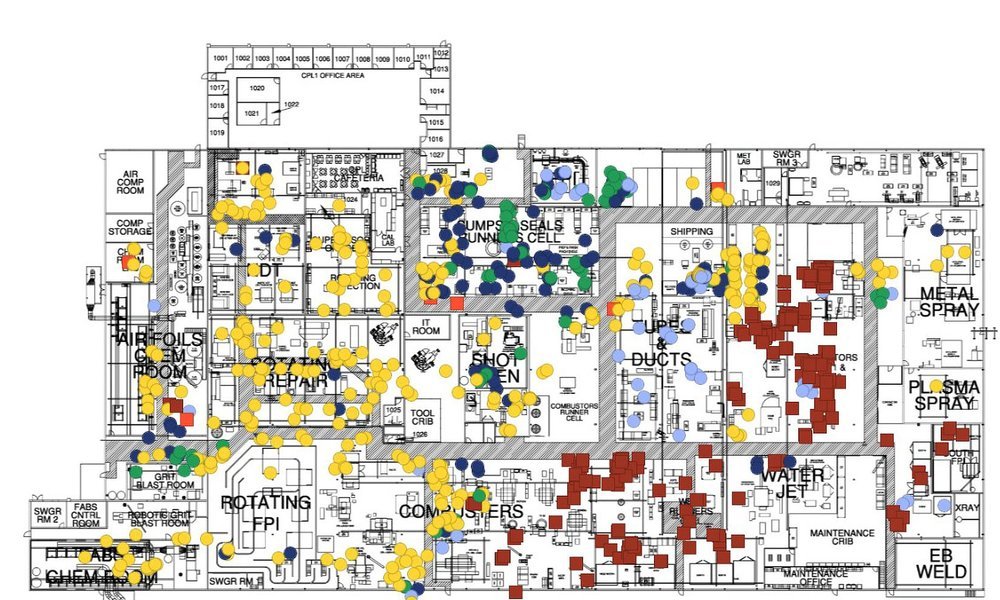
Managing Three Different Tracking Needs Within Crystal Group’s Manufacturing Facility
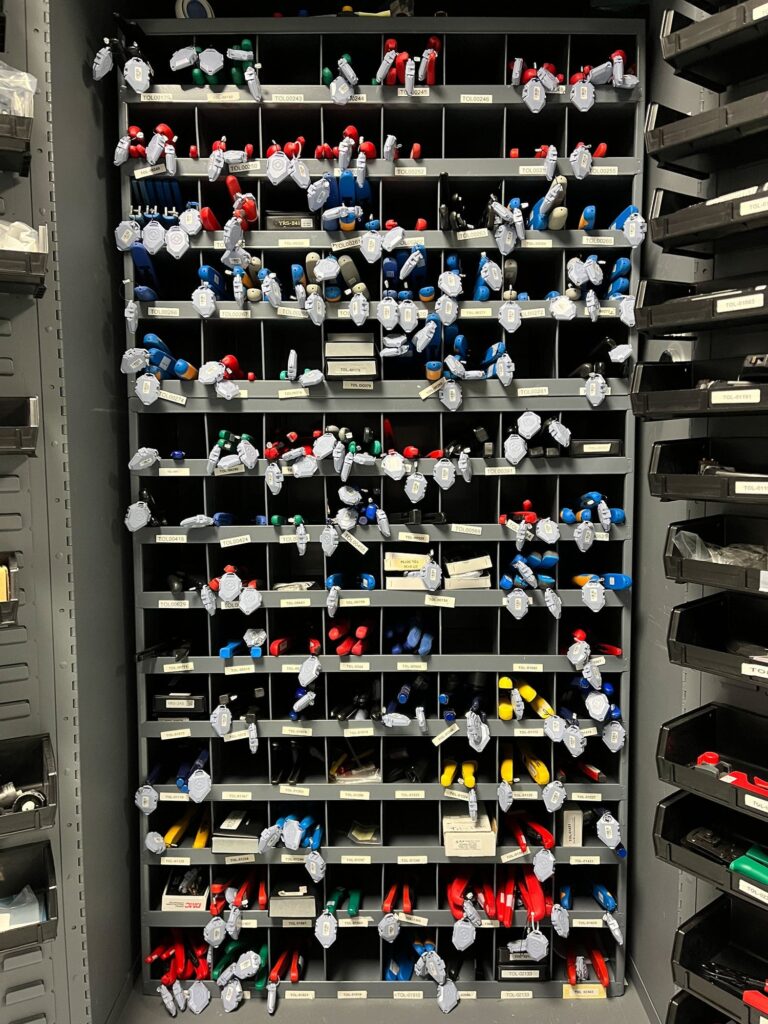
By installing Wiser’s ATLAS location system, ACSC was able to significantly reduce the time spent manually tracking the locations of its work orders. The daily task that previously required 12 people to spend three hours each day was reduced to just 15 to 20 minutes per person. With the system in place, ACSC now has a continuous and accurate overview of the location of all its work orders, eliminating the need for manual searches and estimation.
ACSC evaluated several location systems before selecting the ATLAS system. The MRO facility chose this solution for its accuracy, ease of setup, competitive price point and comprehensive flexibility in the tracking software. After implementing the system facility-wide, the company found that it achieved a return on investment in just three months, improved productivity by a factor of 12 and increased work capacity 15 percent. Furthermore, it boosted worker satisfaction by streamlining the workflow-management process and reducing the workload.
Crystal Group, a leading provider of custom ruggedized computer and network equipment solutions, had three distinct tracking needs within its manufacturing facility. The company required a system to track its 900 assets, including calibrated tools, sales order carts and government-owned assets. The current manual method of tracking with pen and paper was inefficient and time-consuming.
This resulted in the expenditure of a significant amount of time and resources. With many kinds of assets in each category, and with varying movement and tracking protocols required, finding a single tracking solution proved challenging. Crystal Group ultimately adopted Wiser’s UWB solution for the ease and benefits of deploying a single technology to address all three of its disparate tracking needs.
In sum, ultimately, the choice between RFID and UWB technologies depends on the specific use case and requirements of the application. Combining multiple tracking technologies, such as RFID and UWB, can, in many instances, provide more comprehensive and accurate asset tracking. It is important to evaluate not only the specific requirements of your operation, but also which technology or combination of technologies will best meet each of your specific tracking needs.
Article by Cris Masselle, CMO at WISER Systems. This article first appeared in RFID Journal, April 2023.