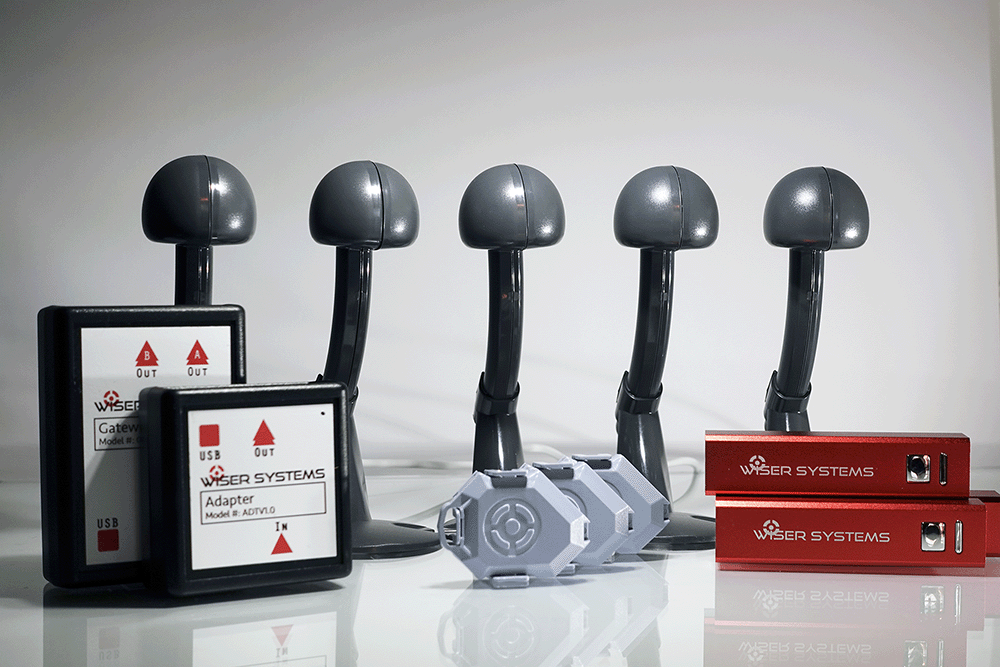
The voice of the internet sometimes makes technologies sound like strange super entities. People talk about AI, Big Data, THE Internet of Things, or Digital Transformation as if they’re universal frameworks that exist only on a grand, finished scale spanning entire cities.
The digital landscape often portrays technologies like AI, Big Data, Industry 4.0, IoT, and Digital Transformation as grandiose, city-spanning frameworks. However, these concepts can also thrive on a much smaller scale, often starting modestly before evolving into groundbreaking innovations.
Real-time location systems (RTLS) exemplify this perfectly. While RTLS can be intricate, requiring extensive equipment, complex installations, and specialized training, they don’t always have to be daunting. WISER’s ultra-wideband (UWB) RTLS is designed to simplify these complexities.
So, what can you achieve with WISER’s compact RTLS evaluation kit?
1. Deploying WISER RTLS in Your Operational Environment
Implementing RTLS in real-world settings differs significantly from controlled lab conditions. Ensuring accurate performance in your specific operational environment is crucial, and it requires comprehensive site testing to address potential challenges.
Operational environments can introduce numerous obstacles, such as:
- Obstructions and clutter
- Limited connectivity
- Radio frequency interference
- Reflective surfaces causing transmission issues or multipath propagation
- Harsh conditions, including exposure to chemicals
- Extreme heat, humidity, dust, or water exposure
- Outdoor elements that encompass all the above
These factors can make RTLS equipment difficult to access for maintenance and restrict where stationary devices, like antenna nodes used in WISER’s ATLAS and Locator systems, can be powered.
Related Content: Using the WISER RTLS in an industrial heavy metal, reflective manufacturing environments.
Each deployment environment is unique, and accommodating these variations is essential for successful RTLS implementation. The WISER system is designed for flexible installations, diverse powering options—including solar power for outdoor settings—and continuous operation without a clear line of sight between devices. Organizations should thoughtfully consider both their goals and the specifics of their deployment environment when exploring RTLS solutions.
The WISER ATLAS and Locator operates the same way with a handful of antennas as it does with dozens or hundreds, so even our shoebox of equipment can be enough to really test whether this system works for an environment in question.
An example: A multinational automotive manufacturer wanted to track bins of parts moving through a welding area. The welding process essentially creates RF noise, posing a threat to RF signal integrity in the vicinity. With just a small deployment of WISER equipment in the area, the manufacturer was able to validate the system’s performance while the welding line operated.
The WISER ATLAS and Locator operates the same way with a handful of antennas as it does with dozens or hundreds, so even our shoebox of equipment can be enough to really test whether this system works for an environment in question.
An example: A multinational automotive manufacturer wanted to track bins of parts moving through a welding area. The welding process essentially creates RF noise, posing a threat to RF signal integrity in the vicinity. With just a small deployment of WISER equipment in the area, the manufacturer was able to validate the system’s performance while the welding line operated.
2. Seamless Data Integration with WISER RTLS
Integrating RTLS data into existing systems can be a complex task. While simply reporting location data is straightforward, interpreting and utilizing that data effectively presents a greater challenge.
For some users, extensive integration into an ERP, MES, or similar software may not be necessary. Basic data access, like searching for a named asset from a tablet, may suffice. In such cases, a pilot project can be used to test the delivery of data without extensive integration.
However, most larger WISER projects involve integrating location data into the customer’s processes via WISER’s API. This integration doesn’t have to be part of a large project; it can begin during the proof-of-concept (POC) phase. Early access to raw location data allows users to experiment with the application of data points, refine the use case, and align the project’s broader objectives from the outset.
For example, a heavy equipment manufacturer had integrated location data with its ERP system. However, their legacy hardware was discontinued and unserviceable. WISER collaborated with the manufacturer to replace the outdated hardware with WISER’s RTLS, utilizing the existing middleware. This approach preserved the manufacturer’s initial investment and allowed WISER’s hardware to function as a seamless drop-in replacement, even before committing to a large-scale project.
For instance: A heavy equipment manufacturer had carefully built a system connecting location data to software tools like its ERP, but their legacy hardware providing that data had been discontinued and was no longer serviceable. When the organization approached WISER about replacing its RTLS hardware, both companies worked together to implement WISER’s location data using the manufacturer’s existing middleware. This preserved the company’s initial investment and made WISER’s hardware effectively a drop-in replacement for the older solution even before the manufacturer committed to a large, long-term project.
Related Content: Exploring RTLS Hardware Integration
3. Prove out a larger use case
There’s a reason few Internet of Things (IoT) projects begin at scale. Pulling the pieces together, making things work, and determining if the project is scalable can all be sticky issues.
Say, for instance, you wanted to track carts or bins moving through a warehouse. Testing at the pilot stage will clarify issues quickly—like if the tracking hardware is too bulky or heavy, or if you’re going to need routine battery recharging that hampers the project’s scalability as more and more assets are added.
System installation, as another example, is often a black box to end users. Installation can require RTLS providers to visit a site in-person anytime the system needs to be adjusted even slightly. A complicated RTLS setup or adjustment process can seriously expand the total cost of ownership. As such, trying a small RTLS pilot can be illuminating not only for system performance but for the scalability and true expense of setting up a larger deployment.
WISER’s system architecture allows for simple, modular scalability. If, in the future, end users need to track additional assets or enlarge the tracking arena, they can add antenna nodes and tracking tags piece by piece without having to redo the setup already in place. This flexible design allows end users to test early, scale incrementally, and keep the project manageable at every stage.
Case in point: A yard management services organization wanted a better system to track vehicle locations precisely in lots or enclosed parking garages where GPS is unavailable. This organization started using a basic setup of several WISER antennas and a few tags. After finding success with a small WISER POC, the organization expanded the project to cover a full lot and began repeating the process at similar locations elsewhere.
Bonus: Location-based time and motion studies
Even just an evaluation kit worth of equipment can be enough to start automating time-motion studies. Such studies could entail quantifying how containers move between workstations, identifying periods of idleness for key equipment, or measuring how bottlenecks occur in a location-based process.
Industrial engineers are often already conducting time-motion studies, generally using manual processes, which can require a great deal of effort and expense. Real-time location cuts out the need for starting or stopping a timer or analyzing hours of footage. It can also eliminate the need for human observation in the moment, since precise location histories will be available afterward to study what’s going on and run analytics to help improve processes.
As an example: A consumer goods manufacturer wanted to see how routine work processes might be optimized. To gather the data desired, they planned to study location-based work processes for short times in several different areas of a site. This meant that the manufacturer needed a solution that could a) provide precise, time-stamped location data, and b) would not require extensive installation or support, since the data-gathering process would be repeated so often in new physical areas. A small set of WISER antennas and tracker tags met this need, allowing the manufacturer to gather data in each focus area and then to deploy or remove the system quickly and repeatedly without much effort.
Ensuring Your RTLS System Delivers as Promised
In summary, the primary goal of an RTLS pilot is to verify the system’s real-world effectiveness. RTLS has a history of unmet expectations, with claims about accuracy, update rates, scalability, and overall performance often falling short. Therefore, finding technologies that truly deliver on their promises is crucial.
The most effective way to achieve this is by moving beyond controlled lab environments and applying RTLS to real business challenges in actual locations. This approach allows you to address potential hiccups and roadblocks directly. By doing so, you can confidently determine that RTLS can effectively solve your specific business problems.