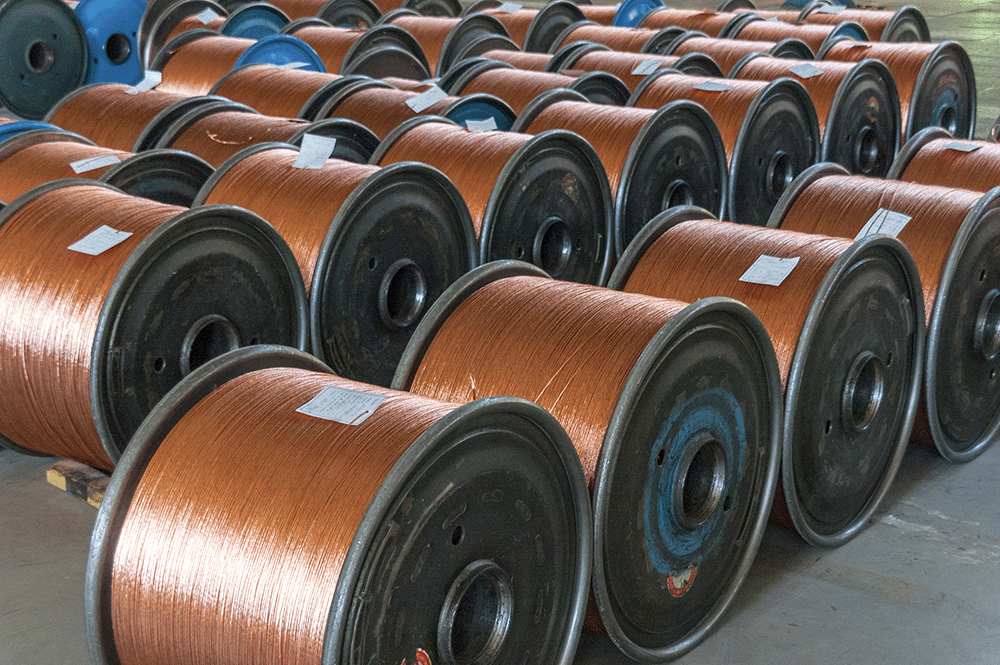
Nearly everyone is familiar with the trouble of losing something important. Leaders in nearly any business are also familiar with the costs and lost revenues associated with searching for and replacing missing assets. It’s no surprise, therefore, that asset tracking has become a top use case for real-time location systems (RTLS) across industries.
How much money do lost inventory really cost a company?
This can be hard to figure out since ‘lost’ assets typically go unmeasured. They’re lost, after all. Furthermore, it’s hard to tell what indirect costs stack up due to missing items.
You may need to do some detective work on how much money missing, damaged, expired, or stolen assets will cost you—and even then RTLS can’t mitigate all of these costs. But this post should help give you a broad view of what losing assets costs across several different industries and use cases. Most of these costs are preventable with the right strategy, process, and technologies in place.
How much do stolen assets cost?
Workplace theft can amount to as much as $50B per year in the U.S. alone. To put that in perspective, the money saved by avoiding these costs would pay close to one million average U.S. workers’ salaries.
There’s plenty to be learned by breaking this figure down more specifically.
Construction
According to the National Equipment Register (NER), construction site theft results in an estimated annual loss of over $1 billion in equipment and tools. The vulnerability of construction sites to theft is a harsh reality that demands proactive security measures.
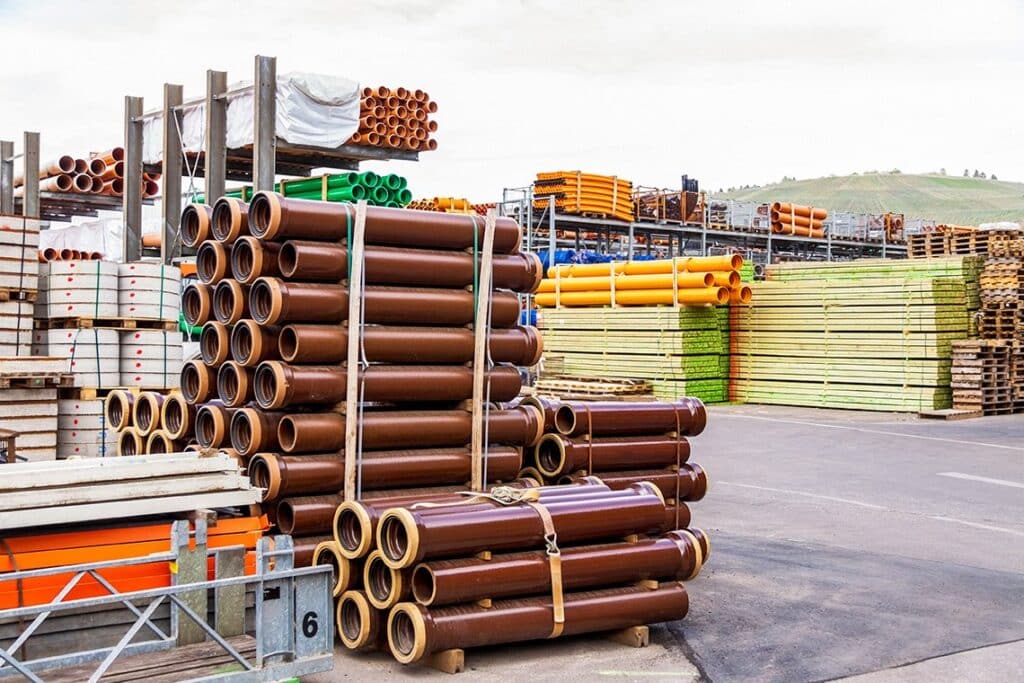
Forklifts
A forklift might seem like a difficult thing to steal, but there’s no shortage of high-profile forklift heists. Some end with property recovery, like the instances of a forklift getting returned to its owners after being driven into the Ohio River or being left on the crime scene after being used to steal an ATM. There’s also the story of an audacious Arizona man who justified forklift theft with the statement, “I wanted it.”
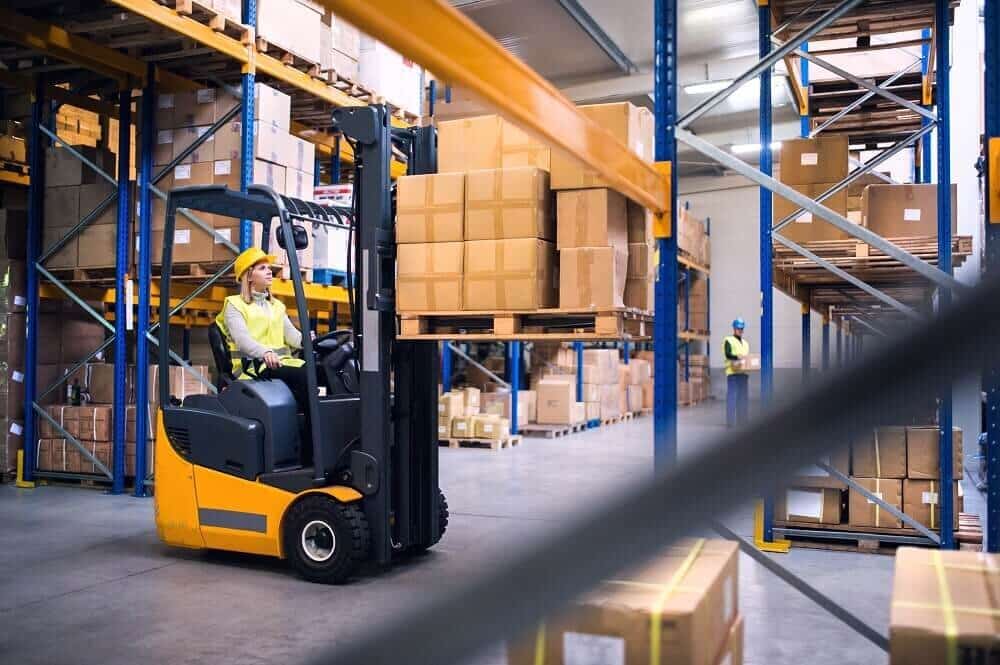
But what do forklifts cost in the first place that makes their theft so expensive? Unit-to-unit, new forklifts cost about the same as a middle-class car.
Vehicles
The United States Department of Transportation reports that over 750,000 drivers experience vehicle theft each year. The dollar amount here likely comes out to about $6B annually.
Laptops
Laptop theft is a big enough problem that it has its own Wikipedia page. The costs here are especially hard to outline since laptops often hold sensitive data, information beyond any sale value. This is a concern for hospitals, airports, and even Government offices.
What about the costs for general inefficiency?
Sometimes assets are only misplaced temporarily or lost internally. It seems like this should cost less than theft, but the numbers are still staggering. In fact, one company found its clients spending 47% of their time “just looking for the right tools.” No matter what the value of the tools might be, that’s a costly inefficiency.
Lost sales
Another WISER customer with a uniform product, online sales, and regular customers reported that after closing a sale their sales personnel spent 40% of their time looking for the specific barcode of the item sold in order to ship it. Thus the company was losing 40% of its sales team’s time, significantly hampering their ability to produce and deliver on additional sales.
Unplanned Downtime in Manufacturing
Losing items is hardly the only cause of unplanned downtime, but it is a persistent one. Unplanned downtime also comes at a hefty cost, ranging anywhere from $30K per hour for a single machine being down to hundreds of thousands of dollars per hour in more extreme cases. All told, unplanned downtime can cost manufacturers up to $50B every year by some calculations. How you can mitigate unplanned downtime?
Shelf-life losses, Cold chain, and shrinkage
Imagine the risks of losing something that could expire when it’s left out too long or gets too warm. This is a massive, expensive problem in cold chain. Better cold chain solutions like precise RTLS could save upward of $150B per year in food product that spoils before delivery. In the very costly pharma sector, around 20% of medicines are ruined because of similar failures in the supply chain.
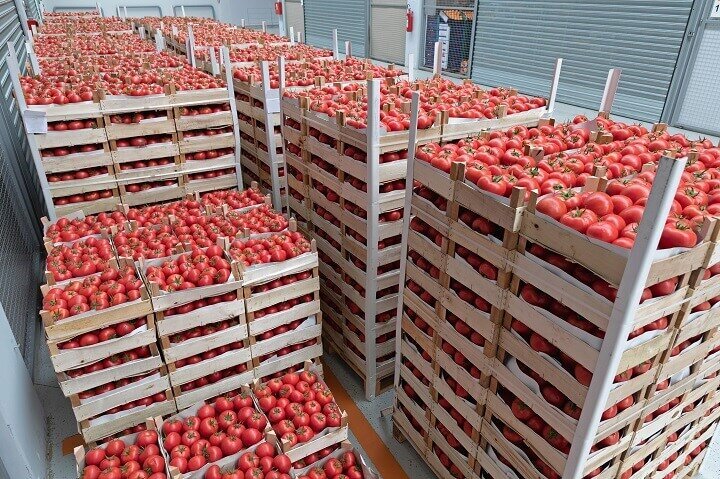
This problem extends beyond agriculture as well. Many products ranging from pharmaceutical goods to roofing shingles sit in warehouses too long and must be disposed of at a total loss. Knowing product expiration dates and real-time location can eliminate waste, shrinkage, and the environmental impact these cause, saving millions of dollars in the process.
Logistics
Logistics processes-gone-wrong cost a fortune every year. Think about any miles vehicles travel beyond what’s actually required. These “empty miles” can cost as much as $20M per year. Further reading: 5 Trends of Digital Transformation in Transportation and Logistics.
Shipping containers lost during ocean voyages account for massive costs as well—$3.5M at a conservative estimate, and possibly more than $20M at the same modest cost per container. Lost pallets are another prime example of expense, tallying somewhere between $750m and $1.5B of monetary waste each year.
How much can I save by improving worker safety?
Worker safety might not seem like a matter of indoor location or precise positioning, but many workplace injuries and accidents are preventable with RTLS solutions focused on the locations of dangerous assets or exposed personnel.
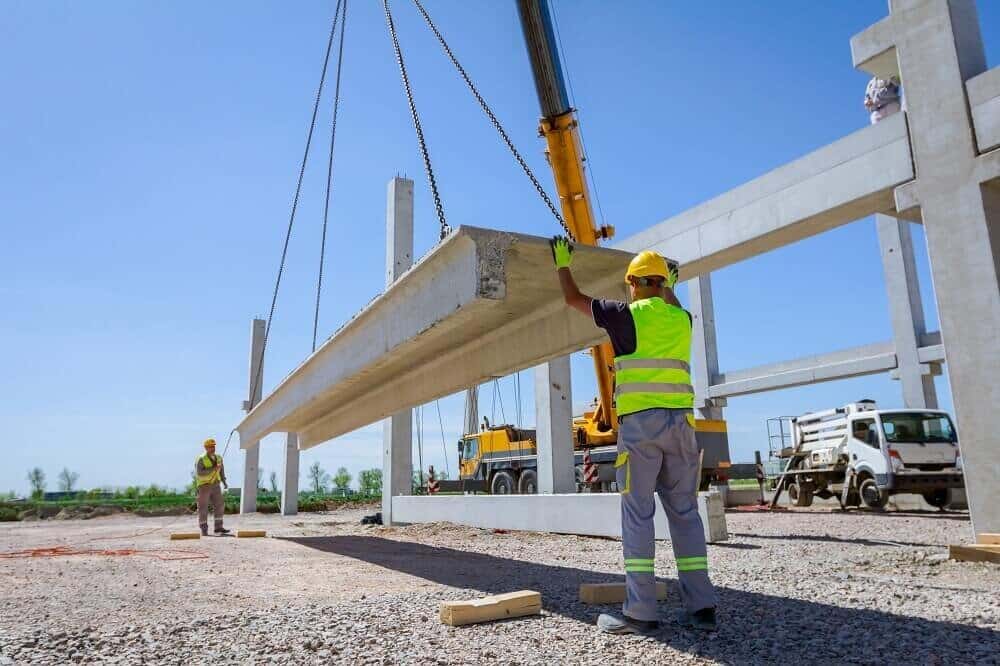
What about added revenues from NOT losing stuff?
Part of calculating the cost of lost or missing assets is calculating what revenues you stand to gain just by improving processes. These revenues could come from speeding up overall production, freeing up more labor hours for alternate tasks, or even from creating new revenue streams not available before. In any case, the potential gains are significant.
Costco’s founder reported that he could cut costs on water bottles by 2-3 cents per bottle if he could simply save one dollar per pallet used to ship those bottles. But the pallets often go missing and are rarely reusable as a result.
Warehousing and distribution applications particularly stand to gain from new revenue streams enabled by accurate asset tracking and location. After all, excess inventory is expensive to maintain. It also limits the overall productivity of a storage or distribution center. Opening up additional space in a warehouse thus translates to added revenues.

In Sum
Any asset loss is costly, and many of the costs of missing items are inestimable. It’s challenging enough just to piece together just how many work processes are disrupted by lost assets, let alone what the value is across the board.
Some costs are clear, though, and many are avoidable. That’s why WISER works to help companies stop losing assets and start saving money.