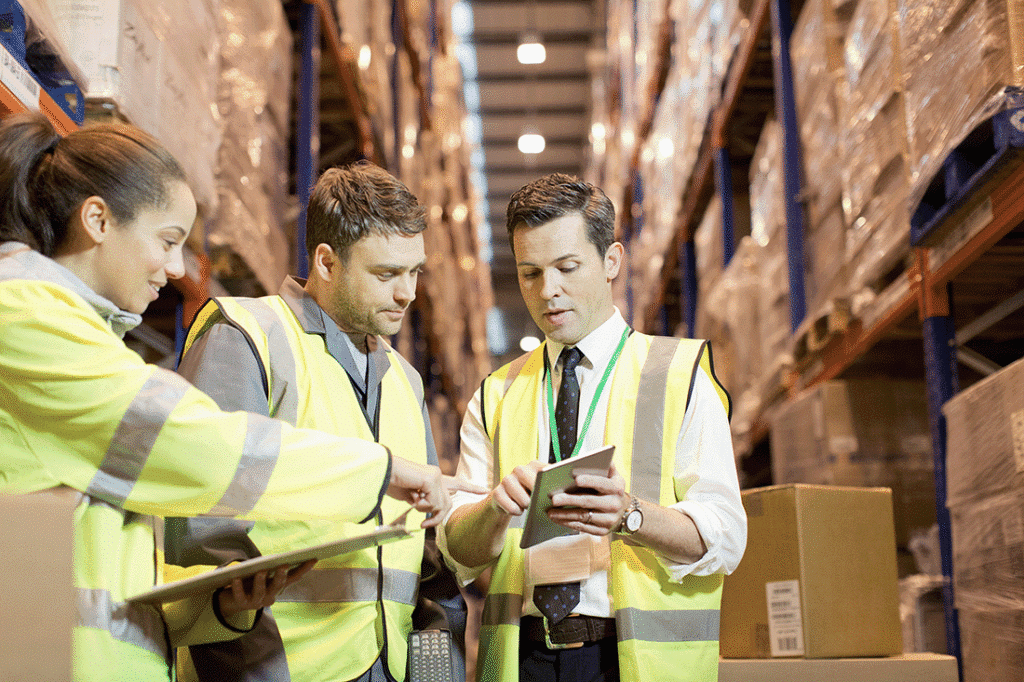
Have you ever thought about what work was like before the computer was a thing? Most of today’s younger workforce won’t remember days before broadband internet. It’s likely that future generations will wonder about a time before work-from-home was feasible.
The point is that technologies change how we work, and many tech solutions are designed specifically to improve our work outputs. This blog post delves into 15 ways Ultra-wideband (UWB) real-time location systems (RTLS) are disrupting manufacturing for the better.
Additional Reading: 25 Ways Real-Time Location Systems (RTLS) Solve Real-World Problems.
UWB RTLS has significantly advanced in recent years, now offering the capability to track thousands of assets simultaneously, a substantial increase from previous limitations of just hundreds. This leap in scalability is driven by the enhanced precision and bandwidth of UWB technology, which allows for more robust signal processing and better spatial resolution. As a result, large manufacturing plants, and sprawling logistics centers can now implement UWB RTLS to monitor extensive inventories and asset movements with unparalleled accuracy.
The ability to track thousands of assets is particularly beneficial for industries that rely on the seamless integration of numerous components and high-value equipment. In manufacturing and logistics, for example, UWB RTLS provides the ability to track a vast number of assets, enhances workflow coordination, minimizes downtime, and supports more efficient supply chain management. Similarly in health care facilities UWB RTLS can ensure that every piece of medical equipment, from infusion pumps to wheelchairs, is accounted for in real-time. This not only optimizes inventory management but also reduces the time spent searching for critical items, thereby improving operational efficiency and patient care. In addition, the scalability of UWB RTLS is a game-changer, providing a comprehensive solution to the growing demands of modern asset management.
One thing to note upfront: Although the points below describe RTLS generally—as if everything is being tracked already—manufacturers can actually choose bits and pieces of nearly every point addressed and can mix and match to what makes the most sense for their organizations.
Work in Progress Tracking
Ultra-wideband (UWB) Real-Time Location Systems (RTLS) are revolutionizing work-in-progress (WIP) tracking in the manufacturing industry. Traditionally, WIP tracking involved manual methods and barcode scanning, which were time-consuming and prone to errors. UWB RTLS changes the game by providing precise, real-time visibility into the exact location and status of materials and components throughout the production process. This technology enables manufacturers to monitor every step of the production line, ensuring that each piece is where it needs to be, when it needs to be there.
The high accuracy and low latency of UWB RTLS mean that even small, rapid movements of components are captured and tracked. This allows for more efficient workflow management, as bottlenecks can be quickly identified and addressed. Additionally, the ability to track WIP in real-time enhances quality control by providing immediate feedback on production issues, reducing waste, and ensuring higher standards of product quality. The granular data provided by UWB RTLS also supports better decision-making and process optimization, ultimately leading to increased productivity and reduced operational costs. In a competitive manufacturing landscape, UWB RTLS offers a significant advantage by streamlining operations and improving overall efficiency.
1. Delivering time and motion data
Manufacturing almost always involves many things moving simultaneously. Whether it’s a batch of parts advancing on the same conveyor belt, a stack of work orders progressing from one station to another, or a worker moving from task to task, the factory is a busy place. One danger is that parts, pieces, or even people can end up in places they shouldn’t. Also, moving from one place to another rarely happens in the most direct, efficient route possible. Thanks to RTLS, manufacturers and other organizations can study actual data on how everything moves.
The patterns behind all these moving parts are invaluable. Real-time location data can illustrate where space can be optimized better. Motion histories can reveal anomalies from normal processes. Timing data can quantify how long each production phase takes without requiring workers to manually account for it. There are dozens of useful ways to leverage a real understanding of time and motion. Today’s factory management “Taylorism” has come a long way since the late 19th century.
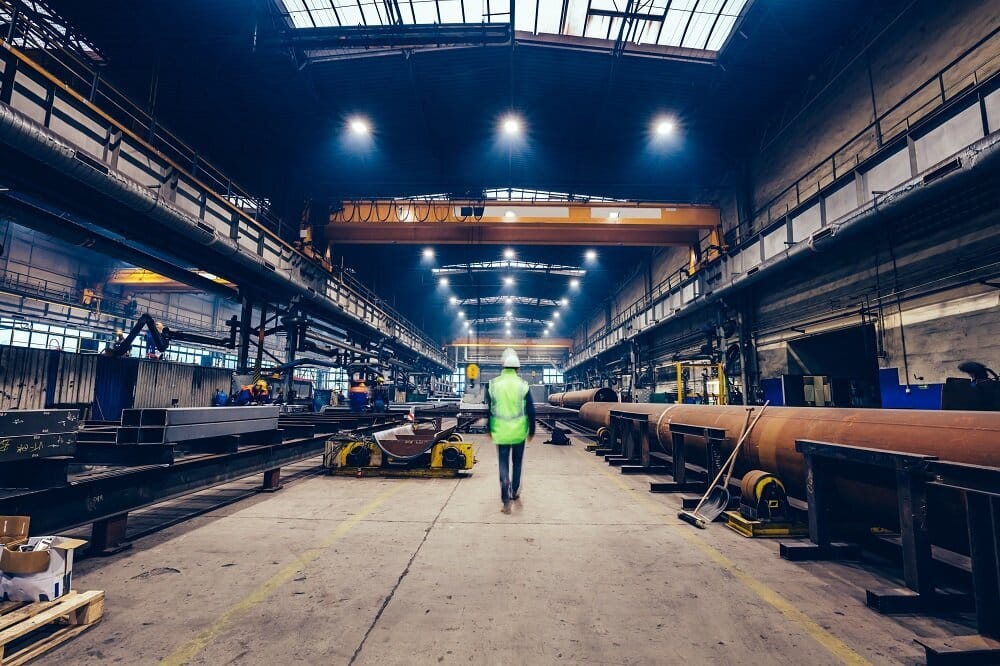
2. Providing early warning signs
Real-time location data can’t identify every possible problem, but asset visibility makes many issues plain right away. For a few examples, consider a pallet of materials inadvertently left at one end of the factory when it’s needed at the other, items on a conveyor belt slowing to half their normal speed, or a perishable item being picked to ship ahead of items nearing the end of their shelf life. The right data can address each of these problems. One real strength of having RTLS in place is the ability to see early warning indicators before they become roadblocks.
3. Generating location-based updates
On the positive side of that same coin, location data can also provide affirmative updates—marking an item’s progression from assembly to quality control, for instance, or triggering status updates as manufactured parts advance from one step to another. Location-based WIP tracking delivers a granular, in-the-moment picture of how far—and in what order—key processes have gone. It also helps reduce the number of manual scans and processes required, as discussed next.
This can be especially valuable for processes involving a steady flow of materials or tools, similar to most automotive manufacturing processes today.
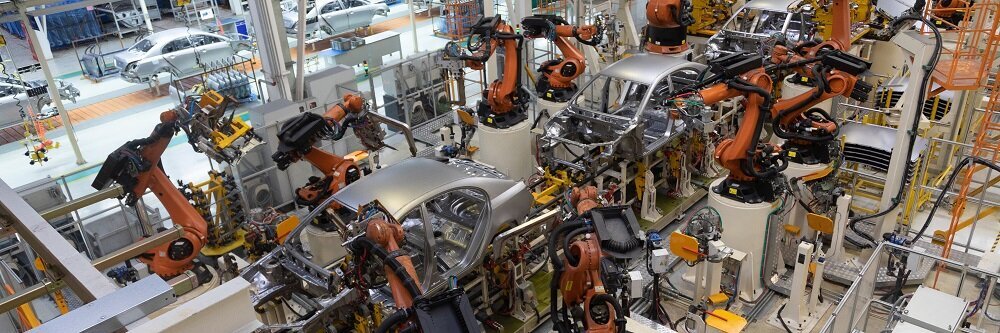
4. Eliminating manual scanning
Scanning solutions like barcodes are ubiquitous in manufacturing. Even in cases where the manufactured part can’t house a barcode itself, factories often institute processes for moving work orders (with individual barcodes) through each stage of manufacturing in time with the item being made.
Scanning is nonetheless a manual process; it’s cumbersome and prone to human error. RTLS can reduce errors with automated, real-time updates—as opposed to updates only at the point of the scan. This makes processes more accurate, efficient, and agile.
Case in point, imagine a 30-step manufacturing process that uses manual scans to log each step. Missing a scanning point could call the entire routine into question if workers don’t catch the error right away. In fact, many manufacturers simply scrap a product if the process missed a key step, since dissembling the item or running a custom operation to fix the mistake is so unwieldy and expensive. By mapping out all the key location points between each scan, it’s possible to actually eliminate the scan itself and proceed with much more confidence in the manufacturing task.
5. Identifying bottlenecks and breaking points
Bottlenecks, chokepoints, or other hurdles between the beginning and the end of a project cost trillions of dollars every year. The good news is many process anomalies are simple and easy to spot proactively, given tools to deliver timing and location data.
As an example, tracking even zone-level location data can show if an item required 10 minutes in the first few stations and 10 hours in the next. More precise location data or tracking histories can help illustrate exactly where and when each delay begins, so that any plans to address them are based on real data and not just a best guess.
Worker Safety
RTLS isn’t the panacea for every risk factory workers face. Dozens of technologies feed into the safety and wellbeing of employees on the job. RTLS fits well into this landscape, however, providing a few unique benefits that are difficult to attain without real-time, dependable location data.
6. Collision Prevention
Although this is one of the more obvious issues for worker safety, companies continue to come up with new collision prevention measures nearly every year. Why? Unfortunately, because harmful collisions keep happening. In fact, worker injuries in total cost factories upward of $167B per annum, with collisions among the leading offenders.
Existing safety measures in this regard include bright signage, audible alerts while vehicles or people move, indoor traffic lights, deployable safety buffers, extensive training, and protective gear for individual workers. What RTLS contributes is in-the-moment data to inform the use of any additional measures.
Here are a few examples: Having a vehicle and a worker approach each other down intersecting hallways could cause lights to come on, or an audio warning to appear, or a haptic alert to trigger on a worker’s person. Rather than having bright, distracting signals flaring constantly, location data can inform other tools at the appropriate time and leave work undisrupted otherwise.
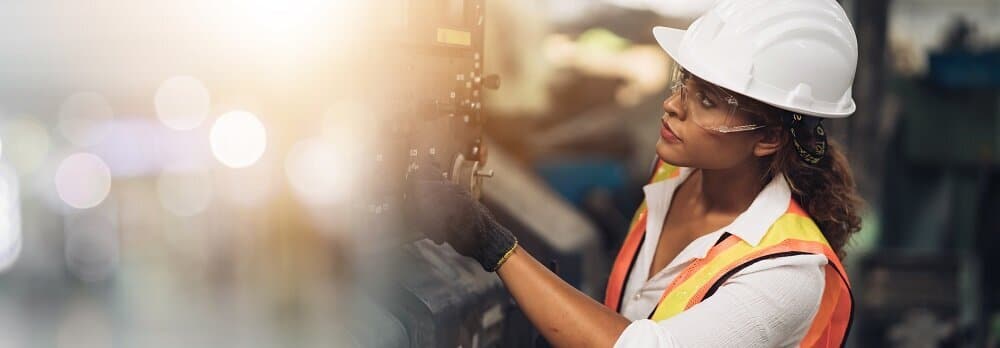
7. Identifying Congested or Dangerous Areas
A big part of collision prevention is identifying the locations where accidents are likely to happen. Location histories can be heatmaps for clogged or hazardous areas. Having a point-by-point trail of where forklifts, pallets, unmanned vehicles, or workers move will immediately show where they share space and how regularly intersection is most likely to occur. This data can then provide insights for whether shifts need to be adjusted, work processes need to change, or even whether a workspace layout itself needs a change to bolster worker safety.
8. Virtual security zoning
Gone are the days when walls, chain-linked paddocks, or locked doors are the only ways to safeguard sensitive areas. Manufacturers can now implement virtual security zoning by simply a) defining the perimeter of a restricted zone and b) choosing who has what access. While virtual perimeters don’t stop contractors or long-term workers from wandering into an area where they shouldn’t be, they can report perimeter violations immediately and automatically, both to workers and to a supervisor.
RTLS makes it possible to delineate restricted zones as items move in real time. An indoor vehicle, for example, could be surrounded by a safety zone that moves with it. Virtual zoning can also eliminate the need for expensive door readers, replacing badge scanning with real-time location data. Furthermore, using location data is generally less personally intrusive than camera or vision-based systems, and RTLS tracking zones can easily be confined to specific workspaces only.
Inventory Management
Keeping track of inventories is a technical challenge for every industry—not just manufacturing. However, smart inventories can be especially important in settings where unplanned downtime can cost hundreds of thousands of dollars each hour, often due to just one or two missing objects.
9. Automating inventory reports
One of the most valuable benefits RTLS provides is its ability to automate inventory reporting. Rather than planning times to shut down operations and check for key tools, hunt for missing items, or individually re-scan materials that never moved in the first place, inventory can become an autonomous, always-current process.
This means that inventory managers can also create customized alerts for when an item leaves its allowed area, when a quantity is low, or when another performance parameter is reached.
10. Cutting paperwork from checkout processes
Checking tools or rental equipment in and out can be a massive headache for environments like factories, where thousands of pieces move every day. Another key way to reduce workloads, prevent theft or loss, and enhance performance is to automate these processes with RTLS.
For instance, by knowing where a worker is and where a key item belongs, it’s possible to simplify the checkout process to one step: picking up the needed item. WISER Systems helped one aerospace plant do just this, by pairing ultra-wideband (UWB) RTLS with their existing processes. The resulting solution eliminated more than a hundred hours of tool inventory management each month.
11. Providing quick search for missing items
Chances are good that you’ve reached for something only to realize it wasn’t where you thought it should be. Whether it’s car keys, a phone, a wallet, or a work order, the problem is the same. It means you have to go looking, retracing your steps, or asking who else might have moved it. For mission-critical items, it might delay vital steps and add waste or danger for every minute lost on the search.
RTLS mitigates this risk by allowing an immediate virtual search for tagged items based on name, ID, category, or virtually any other characteristic. Instead of hitting the factory floor to start the search, factory workers can simply enter the identifying information on a mobile device and see a current picture of where that elusive asset is now. Some wayfinding RTLS solutions even provide a trail from a worker’s current location to the desired item.
Other Possibilities
13. Augmenting other technologies
RTLS doesn’t create a zero-sum game for other technologies. In nearly every case, manufacturers can still use their barcodes or passive RFID, their existing safety systems, their training programs, personal equipment, or any other kind of ‘technology’ while also using real-time, highly precise location technologies.
As an example, WISER helped one manufacturer pair the WISER Locator—an RTLS solution—with a conventional barcode system. This addressed common problems of missing items while building on what already worked. The long and short is that RTLS adds real-time visibility and other capabilities, typically working in tandem with the tools manufacturers already have in place.
For further information how manufacturers can use UWB RTLS with passive RFID, read WISER’s article, Utilizing UWB with RFID: Maximizing Asset Tracking Efficiency.
14. Augmenting existing work processes
It’s also worth noting that RTLS isn’t here to erase the finely-honed ways manufacturers already do things. Because real-time location data reports where things are, rather than mandating where they should be, it can be used to inform, study, assess, or update nearly any work effort involving location, from assembly line processes to quality control to loading and delivery.
In Sum
Manufacturing will probably keep changing as long as people want new things to be made. As such, the 15 points above are just starting positions. Now and in the future, RTLS will save time for workers, help prevent unplanned downtime, and let manufacturers focus on improving their output—the things their workers really need to do.