
Nearly everyone has seen asset tracking. If you’ve visited a well-organized warehouse, checked-out equipment at work, or had your groceries scanned, you’ve seen some form of asset tracking in action.
However, the purpose and power of asset tracking extend far beyond these applications. In fact, solution providers today are devising more and more ways to drive value via asset tracking systems. According to Mordor Intelligence, ASSET TRACKING MARKET – GROWTH, TRENDS, COVID-19 IMPACT, AND FORECASTS (2024 – 2029), “…the global asset tracking market is estimated at USD 23.2 billion in 2024, and is expected to reach USD 43.34 billion by 2029, growing at a CAGR of 13.30% during the forecast period. Asset management and tracking solutions are increasingly critical to achieving greater operational efficiencies in the current market scenario of rapid digitalization in manufacturing environments and office spaces.”
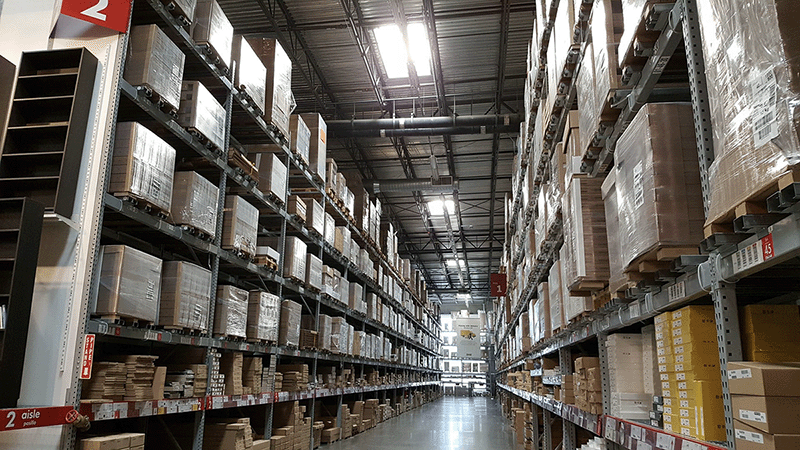
Here are the top things to know about asset tracking in 2024.
Chapter 1: What is asset tracking?
Chapter 2: Technologies behind asset tracking
Chapter 3: The benefits of asset tracking
Chapter 4: Return on investment with asset tracking
Chapter 5: Use Cases
- Asset tracking for smart factories
- Asset tracking for smart warehouses
- Asset tracking for yard management
- Asset tracking for supply chain
Chapter 1: What is Asset Tracking?
Asset tracking gives end users the ability to monitor and manage physical objects, whether in a distribution center, manufacturing facility, a warehouse, or a healthcare setting, to name a few possible scenarios.
Asset tracking typically consists of both hardware and software designed to report physical objects’ status, with a special emphasis on location. Older asset tracking systems usually involve scanning objects to log status updates and provide last-seen / point-of-scan data. Thanks to the emergence of real-time location systems (RTLS), newer asset tracking solutions can follow items’ movement and current location autonomously, providing actionable, point-by-point tracking histories as individual assets move.
With the right tools, it’s possible to track almost any asset that needs monitoring. The purpose of asset tracking is generally to help achieve greater efficiencies, whether in inventory management, manufacturing, supply chain and logistics, or yard management. But the applications go far beyond these few examples, since asset tracking can also include:
- Managing check-in and checkout for company equipment
- Safety applications, such as perimeter breach detection for dangerous items or hazardous substances
- Condition adherence for perishable goods
- Location data for predictive maintenance and repairs
- Retail customer experience
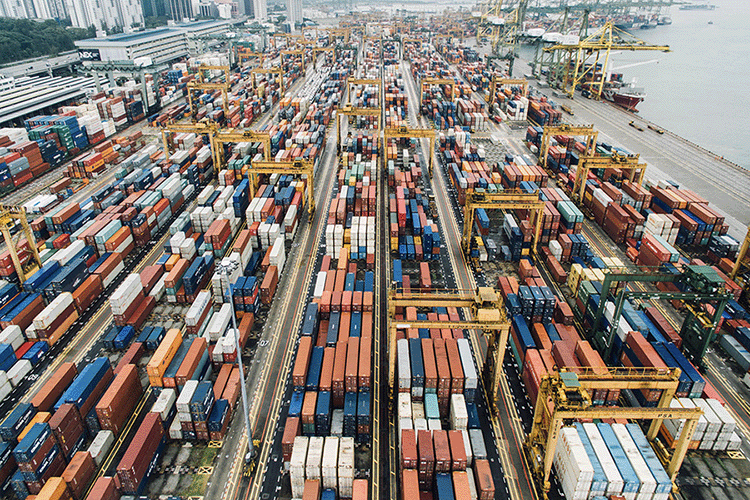
Chapter 2: The technologies behind asset tracking
Finding the right technology can be difficult when implementing a new asset tracking system. First of all, there’s no shortage of options. Second, no single asset tracking technology is perfect (yet) for every individual use case.
As such, choosing the right technology depends on the goals and purposes behind your asset tracking needs. The most common technologies in use today include barcodes, RFID, Bluetooth low energy (BLE), low-power wide-area network (LPWAN) solutions, and ultra-wideband (UWB).
Each technology brings unique characteristics, requirements, and benefits. While barcodes and RFID are ideal for retail settings, as an example, LPWAN technologies are better for fleet management and logistics applications. It helps to consider the following key parameters when choosing the right technology for your business and use case:
- The scope of your asset tracking project, including the size of the physical space and the number of assets being individually tracked
- Cost for each trackable asset; costs and risks for individual asset loss
- Desired update rates for each tracked asset
- Conditions of the physical setting in which you’ll be tracking
- Requirements for collecting and accessing asset metadata
- Costs to deploy and maintain an asset tracking solution
In the end, it’s possible to use most asset tracking technologies harmoniously, perhaps using RFID to manage individual items, UWB to track at the pallet level, and GPS to track the truck carrying those pallets of items. In any case, your requirements for end use will offer the most reliable direction for choosing the right asset tracking technology.
Asset tracking versus RTLS
Asset tracking and RTLS overlap in many instances. In reality, however, both terms describe unique goals and functions that merit some distinction.
RTLS
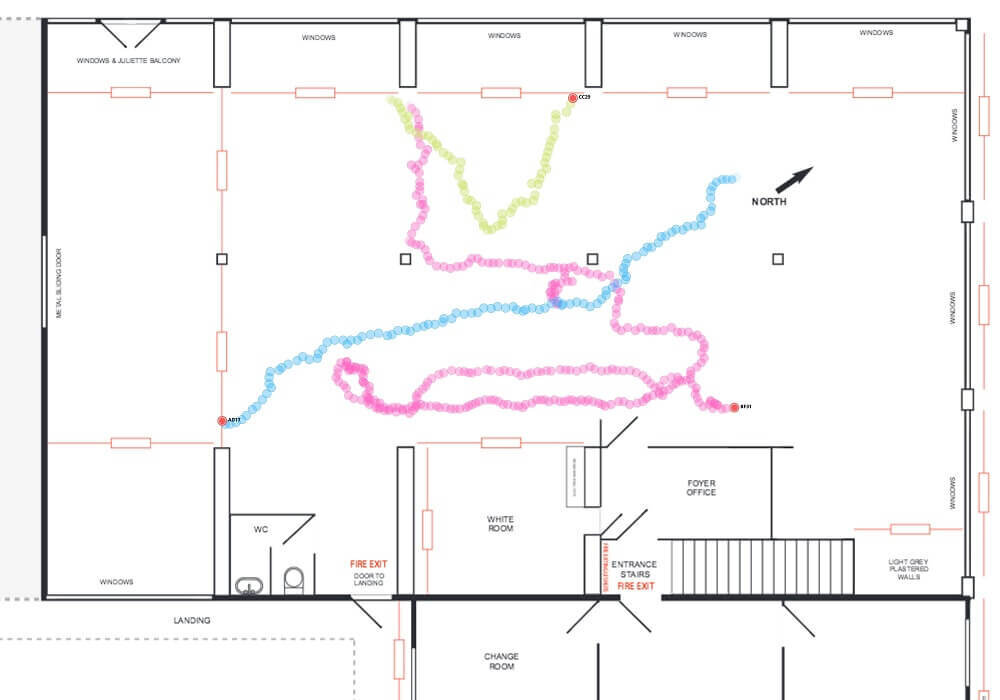
The term RTLS denotes technology solutions for collecting and reporting current, ongoing, immediate location data. RTLS often describes dots on the map—a picture of where something is in the moment. This is distinct from point-of-scan systems, which show where an item was last recorded, or zone-based identification systems, which essentially register whether a specific item is present or not.
RTLS gives immediacy to location data. This helps not only to see what’s happening now but to look back at historical data, studying where an object or person has moved in the past.
In essence, RTLS generates and reports data on the time and place of identifiable tracking devices—data on what, where, and when.
Asset Tracking
Asset tracking is itself a common goal or purpose behind implementing RTLS.
As noted above, asset tracking is concerned with logging and reporting the status of various physical things. Location is often a piece of this puzzle, but many useful asset tracking systems operate without location data as well. Furthermore, asset tracking solutions that do incorporate location might either report in real time or manage status updates at only certain preset points, such as at point-of-scan, transit junctures, chokepoints, or during check-in and check-out protocols.
Asset tracking could be as simple as an inventory list. On the opposite side of the asset tracking spectrum you might find blue dot on the map approach referenced above, where every asset is searchable at any given moment. These two extremes and the many variations between them can be equally valuable, depending on the individual problem being addressed.
Chapter 3: What are the Benefits of Asset Tracking?
If you’re new to the world of asset tracking, it’s well worth asking why it’s important—and understanding how these answers may benefit your own organization.
End users typically employ asset tracking systems to simplify inventory processes and to reduce time spent searching for lost items. These uses tend to apply whether you’re adopting asset tracking for an office building, a shipping center, a hospital, or any other type of workplace. Everyone loses things, and lost inventory isn’t usable. It also costs time and money to search for or replace missing things—not to mention that any time spent hunting for equipment or supplies could be used for value-adding, revenue generating work instead.
The top benefits for implementing asset tracking include:
- Streamlining inventory processes
- Reducing expenses related to lost or stolen goods
- Limiting shrinkage or spoilage losses on assets with expiration dates
- Identifying errors in work processes
- Maximizing work hours for those tasked with finding missing items
- Increasing work output and revenue overall
How these benefits are realized will depend on your own business, what you’re tracking, and how costly asset loss is to your company.
Despite the many cases where asset tracking helps mitigate risks and generate new cash, it’s not a panacea for every operational shortcoming. Asset tracking won’t eliminate the need to physically move and manage key items, for instance. Nor will it remove all human error from your work routines. It will, however, help pinpoint problems in the process.
Further reading: 4 Things Asset Tracking Can Do (and a few it won’t).
Chapter 4: ROI from asset tracking and management
In more practical terms, it’s possible to calculate the real, concrete, specific wins asset tracking brings to fruition.
A recent IBM study found that visibility of connected assets at the enterprise level could a) raise productivity as much as 28%; b) lower inventory repair and maintenance efforts by 17%; and c) eliminate up to 20% of equipment-related downtime.
GE Aviation installed a WISER’s ATLAS, real-time location and tracking system, and according to Kyle Mosier, Site Digital Leader, GE Aviation ACSC, “since installing the system, productivity has increased by 12 times for production control and we’ve been able to increase our capacity by 15%, and reached ROI in three months.”
Other studies and success stories show similar gains. Tom Walker, the founder of Costco, found that he could lower costs on water bottles by 2-3 cents (5 – 25%) of the cost at the time, depending on whether purchasers bought water in bulk or not) just by keeping track of pallets used to move the water bottles.
On the other hand, the costs for untracked items being lost in process are astronomical:
- Approximately $1B of stolen tools in construction each year
- Up to $1.5B annually for lost pallets
- An additional $50B in workplace theft across the U.S. per annum
- Up to $150B each year in cold chain waste
Whether using asset tracking to avoid expense or to increase productivity and revenue, the ROI is becoming clearer and clearer across industries.
Additional reading: Why You Can’t Afford to Lose Assets: A Deep Dive into the Costs.
Chapter 5: Use Cases
Asset Tracking in Practice
The applications for asset tracking are endless. Because the troubles of lost or misplaced items are so universal, it’s impossible to address every area where asset tracking shows its value. A few industries currently lead the pack, however, in terms of putting asset tracking technologies to work.
Asset Tracking in Smart Factories
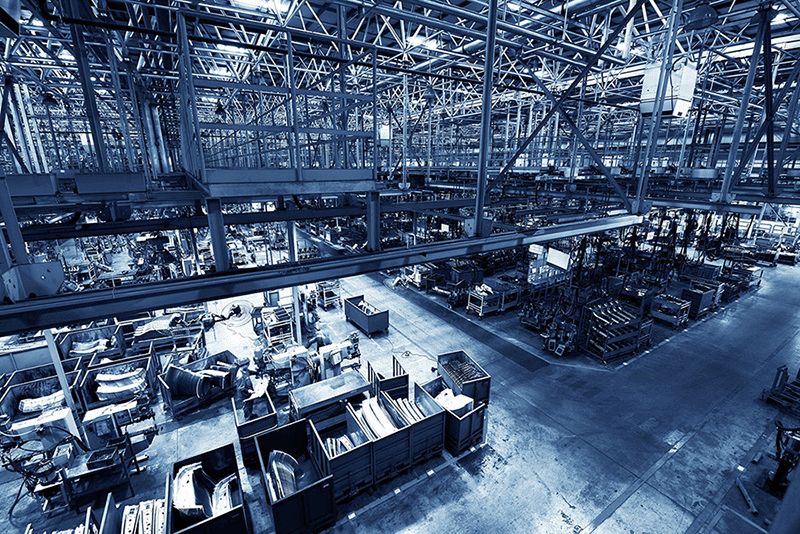
Factories are full of moving pieces. The risk of having any of those pieces go missing (e.g., lost, misplaced, or stolen) are comparably high as well. While missing pieces are a direct source of loss, missing pieces can also result in unplanned downtime, a huge source of loss for any factory. After all, searching for lost materials or equipment and manually updating inventories often disrupts and delays mission critical operations, pulls workers away from other time-sensitive duties, and diverts the attention of supervising personnel.
Asset tracking in smart factories today can involve managing key equipment, valuable tools, raw materials, or goods going through the manufacturing process. Even stationary items, like cranes and robots need to be carefully tracked when they are removed for maintenance or shipped off for repair so they can be correctly maintained and replaced afterward.
Given that timeliness is a critical element in most manufacturing processes, smart factories make an especially good case for asset tracking systems that update autonomously and in real time, rather than traditional point-and-scan solutions or even older clipboard inventories.
Asset Tracking in Smart Warehouses
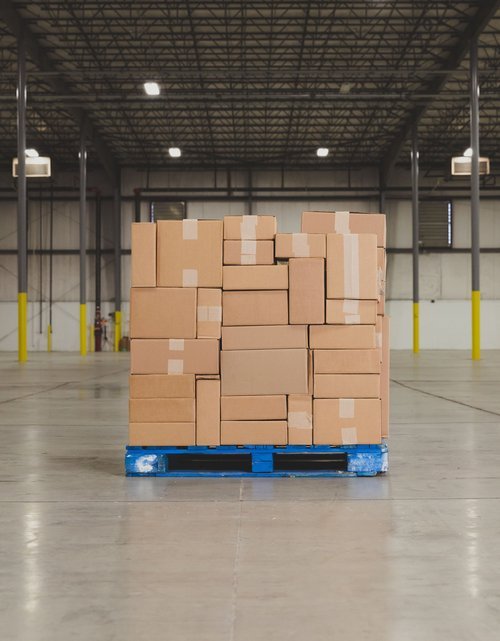
Virtually every warehouse uses some sort of asset tracking system. The very concept of a warehouse demands it, since warehouses exist for managing and maximizing inventory, organizing use of storage space, and making the right things easy to find at the right moment.
Smart warehouses today use a variety of asset tracking systems to manage picking and packing, organization of receivables, accountability for worker equipment, and first-in first-out / last-in first-out (FIFO, LIFO) policies. Asset tracking also helps prevent shrinkage by improving visibility of the locations and expiration timelines for perishable goods. While some warehouses still use clipboards with paper inventory sheets to keep track of what’s where, it’s more and more common to find combinations of barcodes, RFID, augmented reality tools, and RTLS.
The impetus for asset tracking in warehouse settings is almost always to reduce the time spent looking for specific items. After all, hunting through rows of look-alike shelves can expend huge amounts of time and effort.
Additional reading: Combining RFID and UWB Technologies.
Whether at a warehouse, a factory, or a distribution center, yard management depends on timely access to the right vehicle. Finding the right vehicle is often challenging, however, even with GPS devices reporting each vehicle’s general location.
Asset Tracking in Yard Management
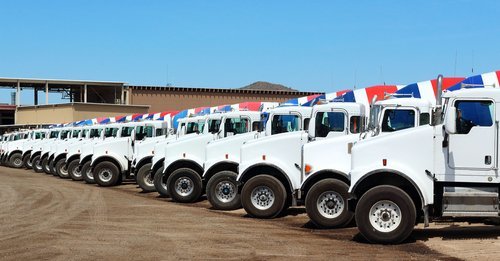
Whether at a warehouse, a factory, or a distribution center, yard management depends on timely access to the right vehicle. Finding the right vehicle is often challenging, however, even with GPS devices reporting each vehicle’s general location.
Because GPS is typically only accurate within several meters, a GPS signal won’t give parking-position accuracy. Also, GPS doesn’t work underground and rarely works anywhere inside a parking deck.
Vehicle accessibility is also a problem. Making every vehicle accessible for a quick departure would require drivers to park with space to spare. But to maximize storage space, it’s common for vehicles to be surrounded during the parking process.
Every lost or inaccessible vehicle introduces delays in starting and finishing a job. First, drivers need to find the correct truck or trailer from among dozens or hundreds of similar models. Next, drivers often need to move neighboring trucks or trailers to gain access.
It’s also possible that multiple drivers will need to work together to make a particular vehicle accessible in a hurry. This precludes those drivers from beginning other jobs in the meantime. Searching and shuffling positions can also congest the lanes of traffic for vehicles entering or exiting the lot for other jobs–and drivers walking the yard pose additional safety problems as other vehicles enter or leave the area.
All these challenges translate into lost time on the job, reduced numbers of jobs completed, and unneeded hassle for yard managers and drivers alike.
For a deep-dive into yard management, read our Complete Guide to Revolutionizing Yard Management: Track Everything in Your Yard.
Asset Tracking in Supply Chains
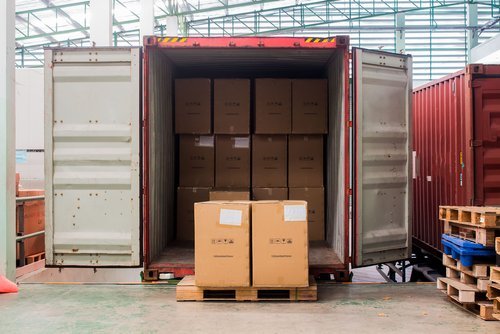
The critical need for asset visibility in supply chains has never been clearer than in the last couple of years. Since supply chain breakdown leads to empty shelves on one hand and overstocked items on the other, improving each stage of the supply chain begins with keeping track of current inventories, inventory needs, and deliverables enroute.
Supply chain management already incorporates a plethora of extremely complex asset tracking systems. For instance, nearly every delivery chain involves multiple handoff junctures—places where items move from a ship to a truck, for instance, or from a pallet of identical boxes into individual deliveries. Primary carriers, manufacturers, and third-party logistics (3PL) companies have carefully managed these junctures for years using connected software tools, barcode scans, shipping manifests, and various other tools.
Asset tracking today also allows for real-time location of the vehicles transporting each deliverable and greater visibility and asset protection at critical turning points in the supply chain. This is only likely to expand and evolve in coming months as just-in-time (JIT) delivery, expirable vaccines, and global disruptions dominate supply chain conversations.
Asset Tracking in Healthcare
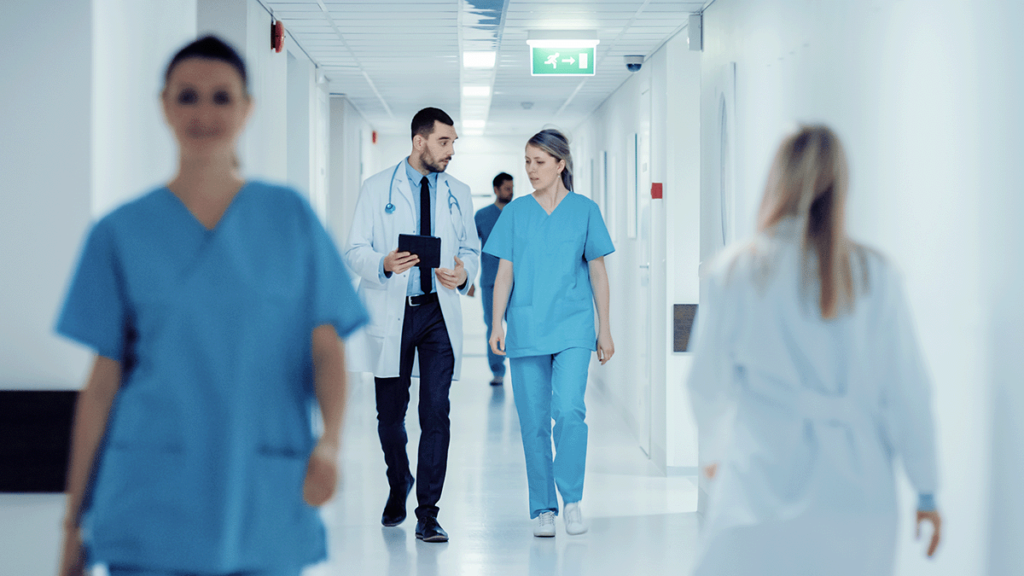
The use of RTLS for asset tracking and management is continuing to rise in the healthcare sector to improve overall productivity and patient safety. Hospitals are developing asset management plans to optimize the workflow of healthcare equipment, staff and patients, leading to improved quality of care and greater efficiencies.
“Hospital Asset Management Market to Advance at CAGR of 9.5% during the forecast period,” according to Transparency Market Research (TMR).
Modern healthcare demands huge numbers of reports. Some reports are only for internal use, but others are for families and loved ones of patients. For instance, families of older adults and extended-stay patients can be concerned when they fail to receive an update on their family member being visited by a nurse or doctor. It’s often the case that physicians can’t report these types of interaction—either to internal managers or authorized family members—until their shifts end hours later. This can leave family members waiting uncomfortably and questioning whether their loved one is receiving needed care.
Healthcare facilities are also full of moving pieces. This includes not just patients and physicians but objects like gurneys, wheelchairs, infusion pumps, defibrillators, and other medical supplies. Many hospitals face the issue of not being able to find a key item when it’s most needed. It’s also common for inventory staff or nurses to discover a surplus of unused supplies and equipment in out-of-the-way closets or under-utilized spaces. Sometimes they don’t discover this until after spending significant funds to purchase additional units.
All these data points and moving pieces require precise record keeping, which takes time away from immediate concerns like patient care.
Physicians and nurses can be outfitted with tracking tags so they can be instantly located during their rounds. This data can show which rooms and procedures consume their time and even which individual station they visit. Such systems can autonomously produce reports of any visits at the very moment they occur.
In Summary
Asset tracking can be very beneficial in streamlining inventory processes, reducing expenses related to lost or stolen goods, identifying errors in work processes, and increasing work output and revenue overall. Whether you need to track inventory in a warehouse, work orders in a manufacturing facility, locate healthcare workers or equipment, or keep your supply chain running smoothly, an asset tracking system can be an invaluable tool. And the most valuable asset tracking tools of all work autonomously, in the background, and in cooperation with existing management information systems/ERP’s while eliminating cumbersome, error-prone manual processes.