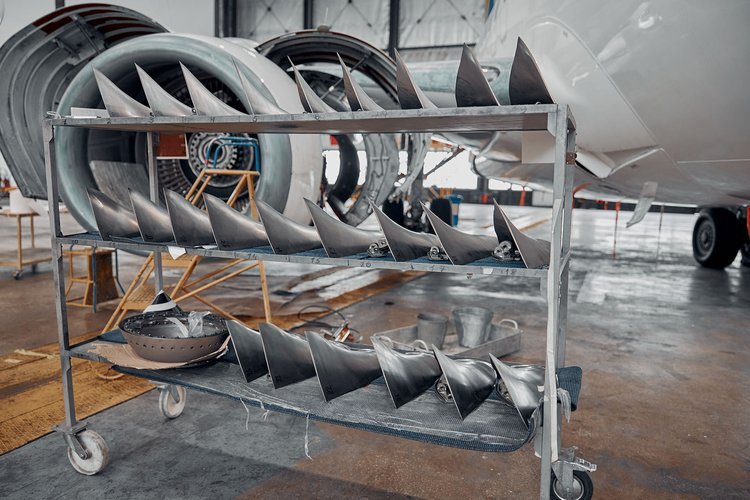
The use of Real Time Location and Tracking Systems (RTLS) in the aviation and aerospace manufacturing and maintenance industries can greatly improve efficiency, productivity, and cost-effectiveness. By providing real-time data on the location and status of work in progress or aircraft parts and maintenance equipment, RTLS can streamline production and maintenance operations, reduce downtime, and improve productivity. Additionally, the cost-saving potential of RTLS is significant, as it can help identify and address inefficiencies in production and maintenance processes, reduce the need for manual labor, and minimize the risk of equipment loss.
RTLS is increasingly being utilized in the aviation industry to effectively track and manage various critical assets, such as costly parts, calibrated tools, and maintenance equipment. By doing so, manufacturers can easily monitor the location and status of these assets throughout the production process, ensuring that they are accounted for at all times. Additionally, RTLS technology can also be used to track and monitor third-party assets, such as expensive calibrated tools or components that may be owned by a third party, such as a customer and/or the government.
The integration of RTLS within the aviation and aerospace sector has the power to transform operations and significantly boost industry performance through increased efficiency, productivity, and cost savings. Implementing RTLS can revolutionize the way the industry functions, improving overall performance and operation.
According to Boeing, the commercial aircraft market is expected to reach $3.9 trillion through 2032. Airbus and Boeing still foresee more than 40,000 new commercial jets needed throughout the next 20 years.This growth is likely to further increase the need for more efficient manufacturing practices, including the use of RTLS in the production process. In aviation this can mean fewer grounded aircraft and added flight time.
In OliverWyman’s 2024 report, “The global aviation maintenance, repair, and overhaul (MRO) market has made considerable progress in recovering from the impact of the COVID-19 pandemic, reaching 98% of the pre-COVID 2019 spending peak in 2023. This year, MRO spending is expected to set a new record of $104 billion. Looking ahead, we predict the MRO industry will expand by an annual rate of 1.8% through 2034, reaching $124 billion.
This guide will explore the use of RTLS in the aviation and aerospace manufacturing and maintenance industry, including:
- What RTLS is and its importance in the Smart Factory, Digital Transformation, and Industry 4.0.
- The different technologies used in RTLS
- How different technologies perform in heavy metal environments
- The use of RTLS in aviation and aerospace manufacturing and maintenance facilities
- The use of RTLS for tracking calibrated tools
What is RTLS and its Importance in the Smart Factory, Digital Transformation and Industry 4.0?
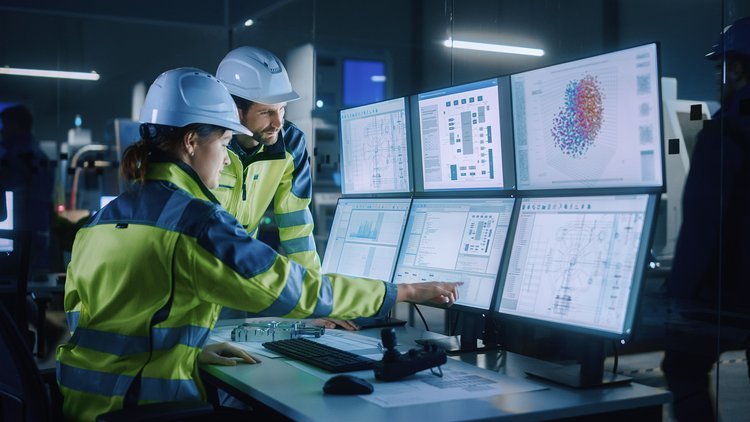
RTLS is a vital technology for the Smart Factory, Digital Transformation, and Industry 4.0. For many organizations, implementing a location solution like RTLS may be the first step in modernizing their factories.
Unlike global positioning systems (GPS), RTLS focuses on localized positioning. While both track time and location, RTLS also includes identification as a key feature, even in situations where identifying information is protected. RTLS provides micro-level positioning where GPS is imprecise — indoors, underground, and in GPS-denied environments, for example.
In simple terms, RTLS provides actionable data on the “what, where, and when” within a defined area. For example, RTLS can show which specific part (what) passed through a particular station (where) during a specific time (when) in a manufacturing process. Another example is RTLS can track which container (what) was loaded onto a specific truck (where) at a specific time (when) during the workday.
It’s crucial to understand that RTLS encompasses a variety of location intelligence technologies. These can include systems that offer proximity-based information or precise coordinates that identify devices at specific points, providing temporary location data at the point of scan, for example. However, for the purpose of this guide, we will be focusing on systems that provide continuous real-time identification, location, and timing data – the “what, where, and when” – as mentioned earlier. It’s important to emphasize that the accuracy of location data is vital to the effectiveness of the data and the usefulness of the RTLS system.
According to MRO Business Today’s MRO Forecast for 2024, “MROs will be faced with the impact of high-interest rates and inflation. The situation would worsen should there be a likelihood of a recession, as naysayers predict. The given backdrop of Geopolitical conflict stresses the situation further, and quick diplomatic/political resolutions are essential to avoid deterioration of the situation, which can impact commercial aviation and all other allied activities.”
Different Technologies Used in RTLS
There are various ways to achieve real-time location tracking, but the most common approach is using radio frequency identification (RFID) technologies, such as WiFi, Bluetooth/Bluetooth Low Energy (BLE) or Ultra-Wideband (UWB).
The basic concept behind an RF approach is the use of tracker labels or tags, to mark and track objects or personnel. A system of reference points, located in known positions, receives transmissions from these tags to calculate the location and/or timing data. These reference points can be referred to as antennas, anchors, beacons, or gates, depending on the system being used.
Some RTLS systems calculate location data at the edge, while others send it back to a server first. Different systems may use signal strength, triangulation or trilateration. Most require a clear line-of-sight between tags, and antennas/beacons/transceivers. Many have varying parameters for hardware installation. The key point is that RF transmissions are the primary mechanism for RTLS across all the most common technologies in use.
In the next section, we will discuss these different technologies and their use in heavy metal environments, such as aviation maintenance facilities.
How Different Technologies Perform in Heavy Metal Environments
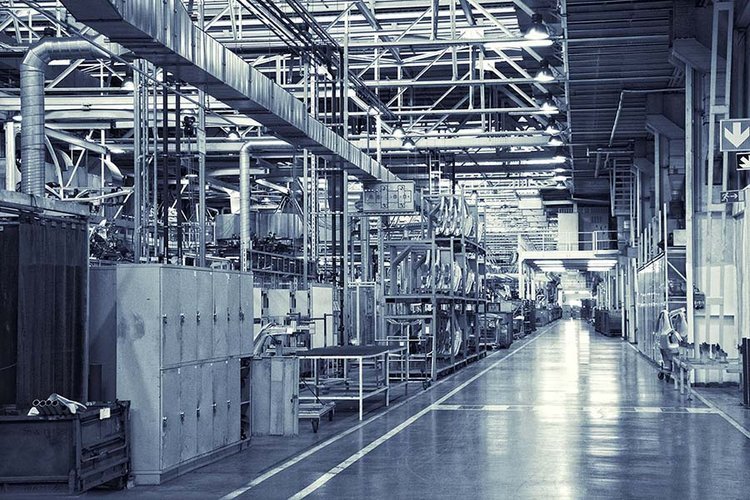
Manufacturing facilities present a unique challenge for RF technologies. These facilities are often busy, noisy places with a high concentration of metal and moving parts. The metal reflects RF signals, and most surfaces weaken or attenuate them.
All RF technologies send out a signal from an object, such as a tag, and a beacon or antenna determines the distance from the signaling device. In a metal-reflective environment, each signal from a tag generates the true direct path and many longer reflected paths. To determine location and distance accurately, the goal is to find the shortest direct path between the signaling tag and the receiving antenna.
Narrow-band RF technologies, such as Wi-Fi, Bluetooth, and Active RFID, find the direct path based on signal strength via Received Signal Strength Indicator (RSSI) technology. However, in a reflective environment, this can lead to inaccurate results. For example, if there is a pile of boxes between the tag and the antenna, the signal will be weaker if it passes through that wall of boxes. The RSSI system will choose the stronger reflected signal, which is the false indirect path, giving an inaccurate location reading. For this reason, these systems often require direct line-of-sight between the tag and antenna.
According to Dr. Seth Hollar, CTO at WISER Systems, “RSSI technology simply cannot achieve high accuracy in a reflective environment. You can set up a mesh of receivers to measure signal strength in a factory setting but there will be too many reflections for it to be accurate. For RSSI to work properly, it would need to be set up outside with no obstacles to get true accuracy.”
In crowded, complex, and reflective environments, such as a factory floor, Ultra-Wideband (UWB) is the best technology for Real-Time Location Systems (RTLS). UWB is a broadband technology that locates via time-domaine technology instead of signal strength. UWB transmits short bursts of broad waves, and the antenna chooses the signal with the shortest arrival time to reach it. If the signal is weakened by passing through a pile of boxes or even a wall it won’t matter. Software algorithms that evaluate the timing of each signal, allow the UWB system to determine which signal is the true direct path and generate an accurate location reading. This enables UWB to perform well in a reflective environment with many obstacles, even without line-of-sight.
This aspect of UWB also allows the technology to perform well in high-ceilinged industrial environments. Bluetooth and Active RFID often have a reading limit of about 20 feet because the signal strength becomes too weak beyond that range to capture accurate readings. Some systems try to compensate by amping up the power. Besides the increased cost and carbon footprint, there may be adverse health implications associated with prolonged exposure to high-powered RF radiation.
Ultra-low power UWB, on the other hand, can accurately read from distances of 100 to 200 feet away, making it a more viable option in high-ceilinged environments like aerospace facilities or hangars. UWB technologies also have the benefit of not interfering with common communication protocols such as Wi-Fi or Bluetooth.
Using RTLS In Aviation and Aerospace Manufacturing and Maintenance Facilities
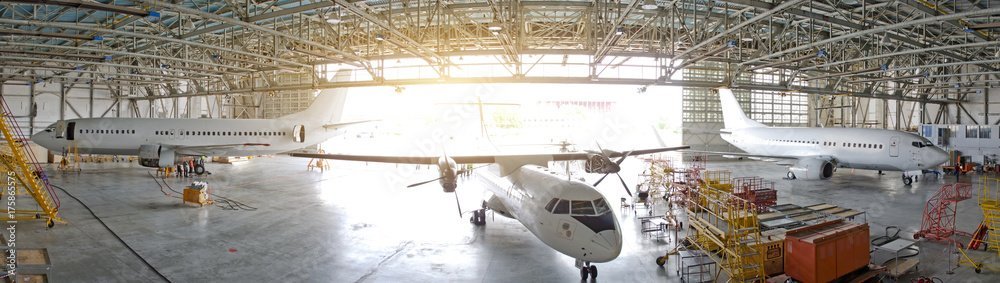
The resurgence of air travel to pre-pandemic levels has brought several challenges to the airline industry, with the aviation and aerospace manufacturing and maintenance, repair, and overhaul (MRO) sector bearing the brunt of this increased demand. This has led to increased workloads for already underfunded and understaffed aviation facilities.
One major challenge for many of these facilities is tracking parts and managing work order flow. These facilities often receive numerous airplane engines and parts daily, which are disassembled and sent to various machine stations for repair across the facility. Tracking thousands of parts/work orders each day without the right technology can be overwhelming.
The pandemic has also led to a shortage of staff, leading facilities to need more efficient workflow management systems that save man hours and make the whole facility more productive.
An accurate, efficient, and simple location system is crucial for these facilities to track their work orders in real-time, giving them a constant overview of their entire shop. With the right RTLS system, facilities can avoid having to manually search for parts based on the final operation performed on them, which can be time-consuming.
RTLS can be used to accurately read current location data, allowing facilities to measure the turn-around times of all parts operations and track work orders entering and exiting each machine. This allows the user to collect weeks’ worth of real data to identify and address bottlenecks in their processes.
Custom zones can also be created to track the movement of process inventory as parts enter and leave established zones, providing a more accurate estimate of when a part will be completed. Additionally, because the engines being maintained may not belong to the aviation facility, it’s essential to track all components as they are shipped to other stations and even other facilities, and then return for final reassembly.
The aviation manufacturing environment is unique for RTLS wireless radio-based systems because achieving high accuracy and adaptability can be challenging. As we mentioned in the previous section, facilities with metal and reflective surfaces need to ensure that the RTLS system they are considering is accurate, secure, flexible, and works in this type of environment, both indoors and outdoors (if needed), and can scale to the required number of assets. Many systems may not be able to do all these functions accurately and reliably in these types of environments.
Using RTLS for Calibrated Tool Tracking
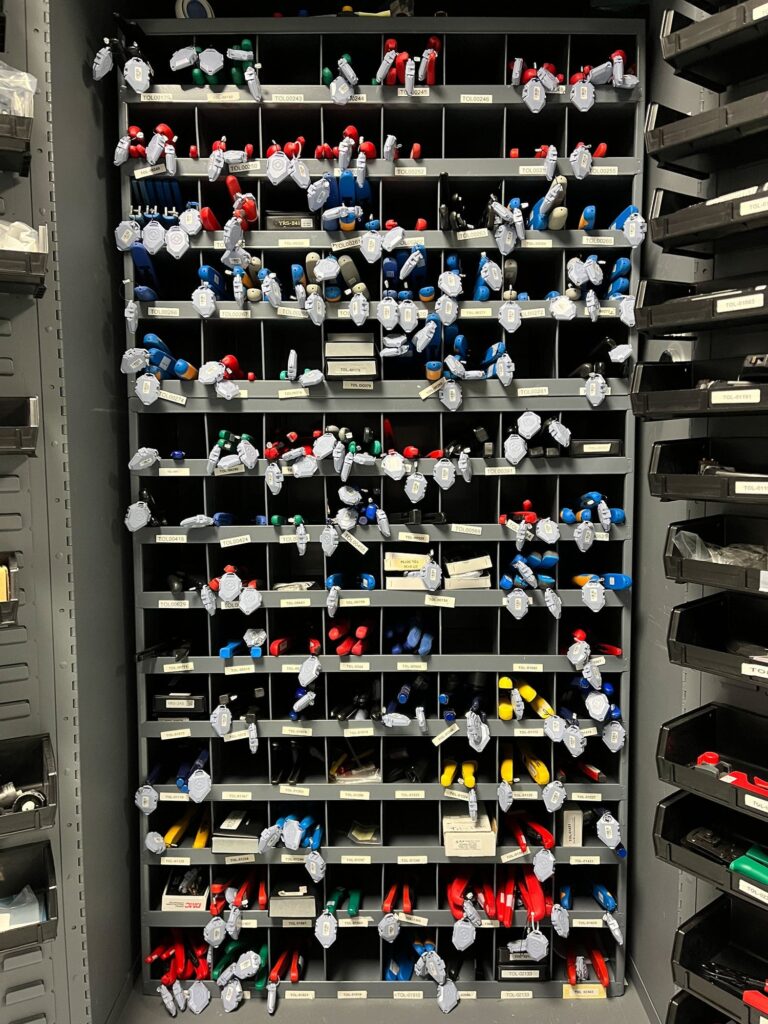
Aviation manufacturing and maintenance professionals are required to perform routine checks of calibration of the equipment, tools, and instruments they use to certify an aircraft or component to ensure accuracy, safety and compliance with industry standards and manufacturer’s specifications. Many aviation facilities have hundreds of calibrated tools that need to be tracked to pinpoint when a particular tool needs to be recalibrated. Searching for a specific calibrated tool in a large manufacturing facility can be an extremely time consuming, manual process. In addition, in some facilities the calibrated tools might not belong to the company, but the government, and they need to always be accounted for.
Misplaced calibrated tools can cause a number of problems. One significant issue is that when a tool is required and cannot be located, maintenance professionals must spend valuable time searching for it, preventing them from performing necessary maintenance on a specific part or piece of equipment. Additionally, some government contracts require facilities to conduct regular and time-consuming inventories of government-owned tools or items. Automating this process can save valuable time and meet compliance requirements.
It is often highly trained technicians who spend their time searching for lost tools; untrained workers cannot dismantle the needed parts to find missing objects. This means that aerospace technicians spend large amounts of time backtracking, repeating their work, or hunting for missing tools when they could be moving on to the next project. The costs in technician time alone are enormous. These costs escalate quickly since searching for missing tools delays deliveries and prevents technicians from undertaking future work as quickly as they are able.
See related article: GE Aviation Improves Operational Productivity, pages 10-11
The utilization of RTLS technology can save countless hours of wasted time. Upfront, employees no longer need to spend time waiting in line to manually check out or return tools, and hours spent searching for lost items on the hangar floor are eliminated. If a tool is not returned at the end of a working shift, end-users can create specific alerts based on who checked the tool out. Some RTLS systems also record tracking histories, providing a granular, inches-accurate trail to follow when finding a lost tool. This means, instead of searching through a large area of the facility, inventory managers and technicians can retrace the specific path along which the tool might have been left.
Zone alerts can also be created to alert a manager if a tool is in an area it shouldn’t be in at the end of the shift. With real-time tool location tracking, even in-transit across multi-hangar facilities, the location of the tools will always be known. Furthermore, it can aid in identifying patterns in tool usage, such as likely places for items to be left behind, or the estimated time required for specific tasks.
According to Deloitte’s 2024 Manufacturing Industry Outlook, “Smart factory and the journey toward the industrial metaverse, Why going smart might be the smartest choice: “…The potential benefits of smart factories are vast—ranging from gains in asset efficiency, labor productivity, and product quality to substantial cost reduction, along with advancement of the cause of safety and sustainability.
In conclusion, to keep your aviation or aerospace manufacturing and maintenance facility running smoothly and productivity high, a digital transformation of your workflow with a UWB locating and tracking system will unquestionably be a competitive advantage. It provides accurate location and distance readings in heavy metal and reflective environments, performs well in high-ceilinged industrial environments, and does not interfere with common communication protocols.